Rotary screw compressors for Australian industry
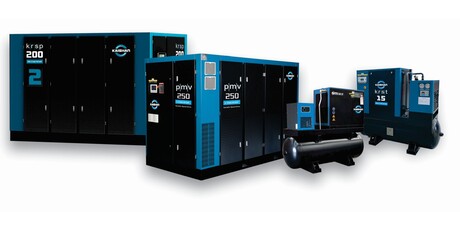
Heavy duty, rotary screw compressors have been the power source of major industries for decades, but like the automobile, though not changing in principle, have come a long way in terms of efficiency, performance and reliability.
New globally developed technologies and engineering advancements mean today’s rotary screw compressors are extraordinary power plants providing high energy output to input ratios. Advanced motor efficiencies combined with new-age single and 2-stage screw configurations provide air compressors that more than meet application demands. Multiple inline compressors can operate huge operations with precise air delivery to meet demand at any time with variable frequency control that automatically limits or shuts off energy intake when not required.
This global development in highly advanced machines has revolutionised the industry to provide a viable, sustainable energy-saving compressed air supply now and into the future.
New compressor innovations include rare earth technology in permanent magnet motors that require far less input power to produce equal or higher air volume output at the application end. Plus the latest developments in variable speed drives eliminate energy wastage through the precise control of compressor air output from nought to maximum, dependent on application demand. VSD programmable air compressor control optimises the co-ordination of the air end, drive motor and compressor to provide much greater air output for far less energy input.
Vast improvements in integrated system configurations and in-line components also add to today’s high efficiency compressed air from the compressor to the application end. These new age air compressors are also much more user friendly, safer to operate and much quieter than superseded types and models.
With outdated compressors not meeting sustainable energy efficiency ratios, new advanced energy saving technologies paired with high-precision engineering and modern, quality-controlled production practices, today’s modern industries can utilise and maintain current and increasing production demands with confidence.
In most cases the dramatic reduction in energy and maintenance bills provides a short investment payback period with ongoing savings and operational efficiency.
Compressors for workshops and specialised applications
Demands from small and specialised industries to reduce energy costs, improve reliability and provide a safe working environment, have created the need for a viable alternative to the old piston type air compressor.
Whilst the piston type, reciprocating air compressor has been the workhorse for workshops and smaller industry applications, they can be somewhat inefficient, expensive and noisy in operation.
New-age alternatives like the advanced scroll, fixed orbit, lubricated compact air compressors offer great benefits over the conventional piston type compressors. Scroll technology has produced a compact air compressor with direct drive and dynamic 3D balancing that delivers quiet, stable and energy efficient performance to far outstrip equivalent piston type, reciprocating machines.
With the added benefit of continuous load capability and an integral aftercooler to reduce moisture carry over, the scroll offers a highly reliable compressed air supply with considerably lower energy bills. The dynamically balanced, non-contact, fixed orbit technology also results in significantly longer element life.
Unlike old piston technology, the scroll includes an advanced digital control panel for ease and safety of operation. This provides operators with monitoring of all key compressor functions, fault detection and protection and service due alerts.
Scroll air compressors give higher output ratios to energy input and with fixed orbit direct drive there are zero transmission losses and no need to oversize the compressor to manage load cycles. The direct drive configuration also means there are no drive belts to wear and replace.
The scroll compressor is available as a standalone, or fully integrated, tank-mounted system complete with large 500 litre receiver tank and optional built in refrigerated dryer and air filter unit. This plug-in, ready-to-use compressed air system saves on independent component purchases, installation costs and floor space while efficiently delivering ample clean air for all applicable industry applications.
Whatever compressed air application demands, from running pneumatic tools to operating heavy industry production lines, these recent advances in compressor and in-line technologies mean Australian businesses can continue to utilise and benefit from this highly efficient and sustainable power source for now and well into the future.
Advanced compressor technology for major aquaculture operations
One of Australia's leading aquaculture companies chose Kaishan PMV rotary screw compressors...
Sydney Water replaces actuators to ensure clean drinking water
Replacing hydraulic actuators with electric actuators from AUMA ensures drinking water is free...
Energy saving air compressors meet food standards requirements
The generation and application of clean, food grade compressed air is critical in food...