PNG showcases world-class technology at Monier's Nebiri quarry
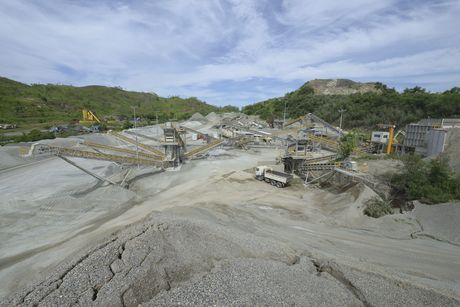
Papua New Guinea has been chosen as the host nation of the 2018 Asia-Pacific Economic Cooperation (APEC) leaders’ summit. This provides the country with the opportunity to boost investor confidence by demonstrating that it has the fundamentals and capabilities to drive sustainable economic growth. 55% of Papua New Guinea’s population is younger than 24 years of age, and 35% of this group is younger than 14. This age distribution is a key indicator of PNG’s high potential for growth and highlights the urgency of attracting investment to enable the rapid development of the county’s infrastructure.
Monier Limited is Papua New Guinea’s single largest producer of construction materials and building products. When the company upgraded its Nebiri Quarry to increase annual output capacity from 300,000 to 1 million tonnes, PNG’s government publicly commended Monier for its contribution to the country’s ability to deliver significant infrastructure improvements.
Currently employing 350 people, Monier supplies ready-mix concrete, quarry products, prestressed and precast concrete products, masonry products and reinforced concrete pipes.
The Nebiri Quarry, which is located in PNG’s National Capital District, supplies the key ingredients that are required for developing infrastructure, including aggregates, road base, armour rock, sand and select fill.
Investing in technology
The decision to invest in upgrading the Nebiri Quarry was made in 2012 so that Monier could be well positioned to take full advantage of the growth in infrastructure that would be generated during preparations for the APEC summit, as well as the ongoing opportunities that the summit may bring. Monier wanted to be seen as a supplier of choice for future infrastructure projects, so it was important for the company to make a good impression on Papua New Guinea’s government and infrastructure developers. With this in mind, Monier focused on a new plant design that would feature a high degree of sophistication, combining record efficiency and high operational standards.
The company aspired to build a highly advanced plant that would be seen by the country’s construction industry as ‘the plant of the future’.
Understanding the operational requirements and constraints
Following a rigorous review of submissions from a significant number of potential suppliers, in July 2013 Monier chose Metso as a strategic partner, awarding the company a €10.5 million contract for the upgrade. The contract included design, fabrication, installation and commissioning of the new plant.
Campbell Johnston, Metso’s director – systems sales and support systems, explained Metso’s approach to the project:
“The plant configuration requested by Monier was not typical. Before attempting any design work for our tender submission, we needed to clearly understand Monier’s space constraints and their operational requirements. We decided that the best way to achieve that was for our engineers to visit site,” he said.
“While sending our engineers over to PNG was a costly exercise, it proved to be a very good move. Based on our team’s firsthand appreciation of site conditions and an exchange of ideas with Monier’s management, they were able to propose an optimised solution.”
Locating the new plant close to the existing plants was a logistical necessity. Land adjacent to the existing plants was allocated, but it didn’t offer the ideal amount of space for a plant that matched Monier’s production requirements. Metso’s proposal was based on an innovative design, which ensured that the new plant would be compact enough to fit into the allocated area.
Project execution and design standards
Delivering the project involved teamwork across three countries: Papua New Guinea, Australia and France. The design and supply of equipment was undertaken by Metso’s team in France. Plant safety had to be in line with Australian OHS regulations and all electrical work was to comply with Australian electrical standards. To best cater for these requirements, Metso Australia took the lead on OHS as well as the plant’s electrical design, installation and commissioning.
In order to comply with Papua New Guinea’s laws, Metso had to set up a local subsidiary. The company’s employees and contractors from outside of Papua New Guinea all needed to have work permits and visas. Setting things up for effective project execution was complex. The process was delayed due to new business and visa procedures that had just been introduced by authorities.
“Customers are not obliged to get involved in a supplier’s logistical problems, but Monier closely partnered with us to get the necessary authorisations. Good collaboration between our two teams is what made all the difference in delivering this complex contract,” said Robert Palmer, Metso’s Australian project manager.
Metso engaged its Australian electrical partner, Peak Industrial Electrical, as well as local PNG companies including SBS Electrical and Workforce, for the construction work. Vincent Gibert, the installation project manager from Metso in France, said: “The key to the success of this project was the excellent cooperation between our multinational team that included representatives from Monier, Metso and our contractors. From the outset, and throughout the project, we performed well together. We shared competencies, information and best practices in each phase, from bid to installation.”
Construction challenges and complexities
With the new plant designed to fit into the allocated space, one problem still remained — there was not enough room for a construction area. Thinking outside the box, Metso gained permission to convert a nearby rugby field into a construction zone.
Equipment was transported from the construction zone to the new site as complete and semicomplete assemblies. Access to the new plant was shared with the existing plants, and so an extraordinary level of project management was required to ensure that the movement of equipment and personnel to the new site would in no way hinder production at the existing plants. This required careful planning and strict scheduling by the project team. Good communication between Monier, Metso and all of the contractors was essential.
Plant configuration and production capabilities
The new plant includes four stages of aggregate crushing and screening. The first three stages consist of three crushers in series, each followed by a triple deck screen. In the final stage, there is the option to send all or part of the product for shaping through a vertical shaft impact crusher. A bonus from this stage is a fine aggregate by-product that can be used as an additive in road base.
The plant simultaneously produces up to nine different products at a rate of 350 tonnes per hour. ‘Made to order’ products have no impact on production rates or quality. To achieve this result, Metso worked closely with Monier’s management to develop a design that offers a unique level of flexibility.
Metso’s design allowed for extra capacity and so Monier was delighted when final tests showed that the plant was capable of delivering the nine different products at a rate of 450 tonnes per hour; 100 tonnes per hour more than the contractual requirement.
Achieving outstanding reliability
During precontract discussions, Monier’s management had expressed concerns about intermittent power cuts that they experience from time to time, mostly without warning. These are caused by unexpected demands on Port Moresby’s electricity grid. Metso addressed these concerns with an electrical design that allows the plant to be run on either mains power or by diesel generator sets. When power is lost, the generators provide power to the plant without the need for connection to the electricity grid.
The system incorporates an uninterruptible power supply that provides backup power for the PLC and SCADA system. A signal appears on the SCADA screen to let the operator know when mains power is lost. The system also lets the operator know when the generators are in operation.
Monier wanted to be assured that the new plant would operate reliably for the next 20 years. To address this, Metso included a five-year Equipment Protection Plan in the contract. Shaun Fanning, Metso’s Australasian head of aggregates explained: “In the unlikely event of component failure we cover all costs, which demonstrates our faith in the reliability of our equipment. This has given Monier a high degree of confidence in the plant’s endurance and performance.”
The plant of the future
“The new plant is very advanced in terms of technology, ease of operation and maintenance,” said Stanley Correa, Monier’s electrical services manager. “On the electrical side, the PLC system design is a real standout for me — from the maintenance diagnostic tools and monitoring equipment that can pinpoint a problem at its source, right down to the compartmentalised layout and the reporting software.”
In operation the plant has proven to be highly efficient, using 40% less power per tonne than the older plants and delivering three times the output of both the existing plants put together. This has been achieved through the combination of the plant’s high production capacity and a unique design that allows production to continue whilst sections of the plant are offline for maintenance.
Anthony Grimmer, Monier’s quarry manager, commented, “In my 35-plus years of mining and quarrying experience throughout Australia and PNG, I have not yet come across the level of sophistication as provided by Metso in the total crushing package at the Nebiri Quarry.
“In my opinion, we can easily claim to have a true ‘plant of the future’. It puts us in a strong position to be selected as a preferred material supplier for PNG’s current and future infrastructure projects,” he said.
Anderson Greenwood Type 84 pressure relief valve
The Anderson Greenwood Type 84 pressure relief valve is designed to protect tanks and vessels...
TESCOM AGI BR Series packaged flushing ring solution
The TESCOM AGI BR Series flushing ring is a packaged solution for flushing and bleeding...
Alfa Laval ThinkTop V55 diaphragm valve control unit
Designed for Alfa Laval diaphragm valves, the slim profile of the ThinkTop V55 is designed to...