Integrated drives for Zambian SAG mills
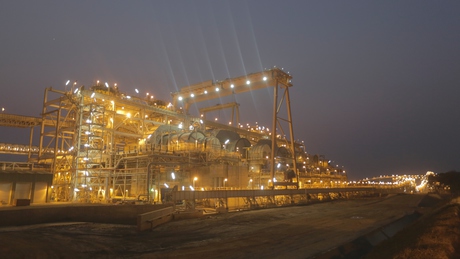
Kalumbila Minerals Ltd., a subsidiary of First Quantum Minerals Ltd., had ambitious output goals for Sentinel, its copper mine development project in north-west Zambia, and needed to recruit an entire workforce to build the infrastructure from scratch all while minimising costs.
Harsh environments, rising energy costs and water scarcity are just a few of the challenges facing the world’s mines. Kalumbila Minerals was not only confronted by these challenges but also had more to grapple with when building two mines in an isolated area 150 km west of Solwezi, Zambia.
The region had practically no infrastructure for transportation or energy supply, and no workforce with the skills to build one. The local population worked in farming and ranching and had no experience with large construction projects. But having committed to source at least half of its workers locally, Kalumbila Minerals needed to find and train at least 4000 people to lay roads, weld pipes, erect pylons and even construct a new airstrip. A further challenge was Kalumbila Minerals’ ambitious production targets: 300,000 tons of copper and 38,000 tons of nickel concentrate per year within the first six years of operation. Meeting this output target would demand advanced drive technology that could power all the mining machinery around the clock with minimal downtime.
To overcome the challenges and make the project a success, Kalumbila Minerals recognised the need for a partner that could offer a solution for both training new workers and providing high-performance integrated drives. End-to-end process optimisation was the only way the company could hope to overcome its production challenges while minimising operational and extraction costs. “For projects involving limited local skills and complex equipment, what we look for in a technology provider is a robust product and a skilled team with the ability to transfer knowledge to our local expert teams,” said Nevin Scagliotta, commissioning manager for First Quantum Minerals’ Projects Division. “With mills of this size, reliable and high-efficiency drives are top priority and crucial to project economics.”
Kalumbila Minerals chose Siemens to provide the drive technology that would give it the power and the cost optimisation it needed. Siemens also knew what steps to take to successfully source and train the new workforce. Kalumbila Minerals recruited 4000 workers from the surrounding towns and hired 4000 indirectly through on-site contractors. Siemens’ project team, comprising professional engineers, assembly supervisors and on-site start-up engineers, then transferred its expert knowledge to the local teams.
Siemens provided the motor and drive systems for two 12 m semi-autogenous grinding (SAG) mills powered by 28 MW gearless mill drives (GMDs) and two 8.5 m ball mills powered by 22 MW GMDs. The integrated GMDs from Siemens provide Kalumbila Minerals with the end-to-end process optimisation essential to maximise efficiency and minimise cost. The drives also provide higher reliability due to the advantages of their gearless design — with no moving gears, there is no variance in the motor and no vibration. This vastly reduces energy loss, as all the force is transferred touch-free via a magnetic field. The lack of moving parts also virtually eliminates wear and tear and the risk of downtime. In the event that maintenance is required, the drives maintain high availability due to their dedicated maintenance modes, such as creeping or inching with rollback of the mill.
“Torque and speed control, and especially the frozen charge protection, keep the mill operating in the safe range, minimise downtime and keep production high,” said Axel Fuchs, project manager at Siemens Process Industries and Drives. “The Siemens GMD offers 28 MW and a 150% overload at 9.1 rpm.”
The integrated drive train came with Simatic PCS 7 and Sinamics SL150 cycloconverter technology. The Simatic PCS 7 controller for the mill drive and Kalumbila Minerals’ existing DCS could be seamlessly integrated due to their common platform, while the Sinamics SL150 offers high overload capacity and efficiency through direct energy transformation, which results in availability of more than 99.5%.
Siemens proved itself to be a trusted partner with the provision of a quality service. This included the professionalism with which its team managed the project and the engineering expertise demonstrated by its gearless drive technology. “For a critical and complex piece of equipment like the mill drives, it is vital to have a self-managing and professional vendor. This is what Siemens has provided with its gearless mill drives and the commissioning team,” said Scagliotta.
Phone: 137 222
Anderson Greenwood Type 84 pressure relief valve
The Anderson Greenwood Type 84 pressure relief valve is designed to protect tanks and vessels...
TESCOM AGI BR Series packaged flushing ring solution
The TESCOM AGI BR Series flushing ring is a packaged solution for flushing and bleeding...
Alfa Laval ThinkTop V55 diaphragm valve control unit
Designed for Alfa Laval diaphragm valves, the slim profile of the ThinkTop V55 is designed to...