Converting oilfield gas flares into revenue
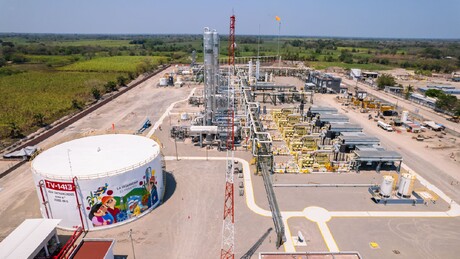
Whenever crude oil is extracted, water, sand and natural gas are part of the mixture. And when large reserves were discovered in the Ixachi field south of Veracruz, Mexico, extracting and transporting the oil was the relatively easy part: separating and shipping the oil via pipeline is always fairly straightforward. Managing the natural gas is another matter.
“Oil is handled like a liquid and transported by pipeline or truck,” said Mudar Jamal Eddin, Engineering Director, Grupo Nuvoil. “Natural gas must be processed and compressed before it can be transported in commercial pipelines.”
If a processing plant is not accessible, producers typically ignite or ‘flare’ the natural gas to dispose of it. This practice is both wasteful and raises environmental concerns. Flaring also represents a lost source of revenue for oilfield operators. To keep flaring to the minimum and maximise returns, Ixachi operators called on Nuvoil to deliver a gas conditioning plant near the oilfield as quickly as possible. Nuvoil is a leading energy services and solutions provider headquartered in Veracruz.
The scope of work for the gas conditioning plant included engineering, procurement and construction — and later operation and maintenance of the completed plant. Located on 13 hA about 16 km from the well pad, the completed Papan Gas Processing Plant was specified to process 9.77 million standard cubic metres (Sm3) of natural gas per day.
A typical timeline for a similar project is two to three years. Nuvoil was asked to complete the plant in nine months.
“While the timeline was challenging, we knew we had the capacity to meet our customer’s needs,” Eddin said. “We had built similar plants in the past, and flare avoidance is our core business.”
To meet customer requirements, Nuvoil designed a cryogenic gas processing system. The complexity of the system is difficult to overstate.
At the wellhead, oil, water, sand and natural gas are separated. The resulting sour gas, which contains sulfur, enters the Papan Gas Processing Plant at about 93°C. In the first step, the gas is chilled to 49°C and residual sand and dirt are separated.
Next, the gas enters the sweetening plant, where sulfur is removed, and then moves to a molecular sieve dehydration system, where humidity is absorbed. In the subsequent chilling process, the gas temperature drops to about -85°C.
“Chilling triggers gas condensation,” Eddin said. “As a result, we can remove LPG (propane/butanes) and other hydrocarbons. What remains is almost pure methane and ethane.”
Finally, the gas is compressed for transport via commercial pipelines.
To speed implementation of the plant, Nuvoil selected a control system integrator they had successfully worked with in the past, Ascend Automation & Controls. Ascend is a division of CAM Integrated Solutions and a member of the Rockwell Automation PartnerNetwork program.
“Our company is very familiar with gas conditioning systems,” said Horacio Tinoco, Vice President, Ascend Automation & Controls. “We developed a control system for Nuvoil about 11 years ago. Of course, the new system enables even more sophisticated and efficient operation.”
The Rockwell Automation control platform is based on Allen‑Bradley ControlLogix process controllers and a FactoryTalk View HMI. To ease system monitoring, Nuvoil relies on a video wall in the plant featuring twelve 55″ displays and four operator workstations in the control room.
To manage the process, more than 3000 instruments are physically connected to the system — and nearly 150 PID loops are included.
In the near future, Ascend will be adding FactoryTalk Historian software to the system: “First, we focused on getting the plant up and running,” Tinoco said. “Now, we are aiming to provide long-term data storage capabilities so Nuvoil can run analytics for multiple purposes.”
Nuvoil completed the plant in the required time of nine months and was running at full capacity within 13 months. Today, the plant processes about 9000 Sm3 of gas daily, representing revenue of about US$200,000 each day.
“When oilfield operators flare gas, they are burning resources — and burning money,” Tinoco said. “Gas conditioning facilities open up an additional source of revenue.”
Ascend looks forward to a continued partnership with Nuvoil as they continue to optimise plant operations.
“Currently, we are exploring artificial intelligence (AI) options to enhance efficiency,” Eddin said. “We are evaluating our exact needs so we can match it with the products that Rockwell Automation offers — and add those capabilities.”
Phone: 03 9757 1111
Anderson Greenwood Type 84 pressure relief valve
The Anderson Greenwood Type 84 pressure relief valve is designed to protect tanks and vessels...
TESCOM AGI BR Series packaged flushing ring solution
The TESCOM AGI BR Series flushing ring is a packaged solution for flushing and bleeding...
Alfa Laval ThinkTop V55 diaphragm valve control unit
Designed for Alfa Laval diaphragm valves, the slim profile of the ThinkTop V55 is designed to...