Clever boxing: Oji opts for energy efficiency in Yatala
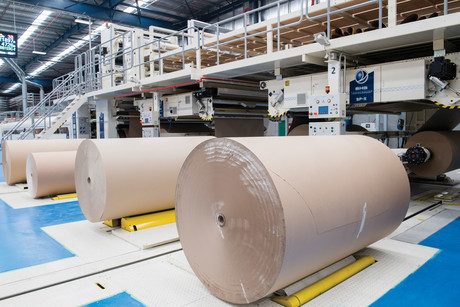
Oji Fibre Solutions is part of the pulp and paper division of Oji Holdings Corporation — the world’s fifth-largest pulp and paper company. From fresh fruit and produce, meat, poultry, seafood and beverages to reseller and industrial manufacturing, the wide range of industries that Oji Fibre Solutions has been supplying innovative corrugated cardboard packaging solutions to in Australia and New Zealand is immense.
As part of the company’s expansion of its packaging business in Australasia, Oji recently invested in the development of a new 5.8 hectare site in Yatala, Queensland. Complementing the company’s existing manufacturing plants in Melbourne and Sydney, the Yatala site houses a newly constructed 2.4-hectare manufacturing facility. From here Oji manufactures and supplies innovative corrugated cardboard packaging solutions to its customers throughout Queensland, northern New South Wales and the Northern Territory.
As part of Oji’s commitment to delivering innovative and environmentally sustainable products, the facility operates to a green-star rating system. From daylight sensors and a lighting control system to a rainwater harvesting system, Oji implemented a number of initiatives that would assist them in reducing emissions and increasing energy efficiency throughout the operation. It is no surprise then that in designing and building the new manufacturing facility, they also chose to invest in the latest and most energy-efficient manufacturing technology.
Energy efficiency was therefore a key criteria for Oji Engineering Manager Peter Henley when selecting the compressed air system for the new facility. From material handling to the conveyor systems, pre-feeders and corrugator, compressed air would be a key utility required throughout the manufacturing process.
After considering a number of vendor packages, Oji chose to invest in a Kaeser compressed air system, consisting of a Kaeser CSD 85 series fixed speed rotary screw compressor, and a CSD 125 SFC Sigma frequency controlled rotary screw compressor, in addition to a comprehensive compressed air treatment package.
A frequency controlled rotary screw compressor was selected as part of the compressed air package in order to meet the fluctuating demands for compressed air of the new manufacturing facility in the most efficient way possible. As the lead compressor, the CSD 125 SFC is responsible for supplying the site’s initial requirements for compressed air.
The inclusion of the Sigma Control 2 compressor controller also enables compressor performance to be precisely matched to actual air demand, thereby allowing additional energy savings.
In any compressed air installation where a frequency controlled compressor is installed, this will be the compressor that operates longer than any other unit within the system. With frequency control, the operating pressure can be consistently maintained with ±0.1 bar. In turn, the consequent ability to reduce maximum system pressure also reduces energy costs. With the CSD 125 SFC, Oji technicians can view the relationship between pressure consistency and speed directly on the Sigma Control 2 display.
Due to the ability to provide a soft rise in motor starting current from zero to full load without current spikes when using frequency control, there is no effective limit to the number of possible motor starts within a given time period because overheating is prevented. The continuously variable acceleration and deceleration significantly reduces component stress.
The additional fixed speed Kaeser CSD 85 series rotary screw compressor at Oji was installed to act as the lag compressor. This means that it only starts up and produces compressed air when the demand exceeds that which the CSD 125 can produce alone. This therefore ensures that the fixed speed unit is not operating in a loaded state for extended periods of time. The result of this configuration for Oji is optimum energy efficiency, reducing power costs, by only producing the precise amount of compressed air required at any one time.
“We have been using Kaeser compressors for some time now on our other sites,” said Henley. “They have proven to suit our application and be reliable and efficient in meeting our compressed air requirements. We have also found that they are well suited to operating in the Australian climate.”
Phone: 1800 640 611
Emerson AVENTICS Series XV pneumatic valves
Emerson's AVENTICS Series XV pneumatic valves are designed with interoperability in mind.
Festo VTEP proportional valve terminal
The VTEP proportional valve terminal uses high-precision piezo valves to reduce compressed air...
Kaeser CSG.1 oil-free rotary screw compressors
The CSG.1 rotary screw compressors have air flow rates ranging from 4 to 15 m³/min and...