Managing corrosion to create margin
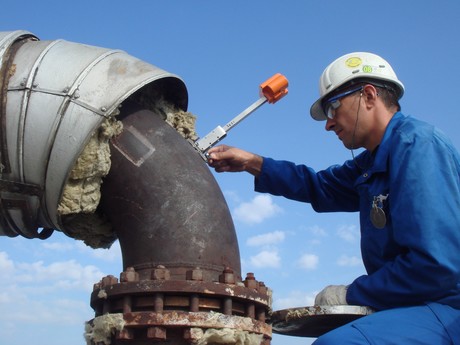
For many industries, raw materials are natural products that vary in quality, creating risk to output quality, risk to plant efficiency and risk to plant reliability. If you can manage the risks, then you can create a profit margin where competitors cannot.
Plants with process control systems designed to handle product variability are positioned to source raw materials that come on to the market at the most attractive price. However, product variability can also mean variation in risk to the plant.
Corrosion is a common problem faced by many industries. Often the raw material itself may be corrosive, or may require processing by potentially corrosive chemicals. In some instances, the material’s potential to corrode can change at elevated temperatures or when it contacts water.
Dosing to neutralise process streams and the insertion of sacrificial coupons into a process stream go some way to managing and monitoring corrosion. Controlling pH reduces the likelihood that a process stream will cause damage and fluid corrosivity affecting a coupon will indicate the likelihood that damage is happening to similar metals in the plant. Neither method, however, measures actual metal loss to critical assets.
Pipework, one of the most common pieces of metallic equipment in processing plants, will sustain loss from harsh products and at some point, will need replacement. As varying products pass through a plant, the rate of corrosion will change so it is difficult to extrapolate a simple rate of change into a useful service life duration to determine an accurate replacement date.
Manual testing
Equipment in plants corrodes (or sometimes erodes) from the inside out, potentially reaching its failure point without any external indication. An unchecked pipe can therefore fail at any time, with disastrous results.
The health of fixed equipment such as pipes and vessels is traditionally measured by taking manual readings of pipe wall thickness. Manual readings require staff to enter the plant at scheduled intervals, require the installation and removal of scaffolding and the removal and replacement of any lagging.
There is no guarantee that a set of manual tests, often taken months or years apart, are readings from the same precise location on a pipe, by the same person, with the same measurement tool. Changes in location, staff and equipment increase variability, reducing precision. Without a high precision measurement, you cannot provide a precise estimate of useful life.
Online monitoring
Over 160 plant operators have turned to Emerson’s Permasense solution to improve precision of corrosion monitoring. The Permasense non-invasive sensors attach to critical areas of pipework on the outside and report thickness measurements twice daily. A central server adjusts the reading for temperature and inspects the measurement provided for noise, which is indicative of changes in the inner surface of the pipe — a common precursor to actual wall loss. With this quality and frequency of readings, in exactly the same location by the same instrument, and without any human intervention, extremely high precision measurements of rates of metal loss can be determined.
Operators can now monitor the impact of corrosion, to a per-batch level, adjusting corrosion mitigation processes and scheduling maintenance as required. Metal loss management then becomes part of the operational process control rather than just part of the maintenance process. Operators can be proactive about what raw materials they process and how they approach each batch, backed by precise up-to-date knowledge of the condition of their plant, and how it is impacted by varying raw materials. Managing these risks allows operators to choose which products and process decisions will provide them with the healthiest profit margins, without unplanned outages or loss of containment.
A live webinar on the topic of pipework monitoring will be presented on the 11th of August. Register at http://emr.sn/5WB4.
Reducing emissions from industrial processes by effective particulate monitoring
Continuous particulate monitoring instruments play an important role in air pollution control.
How to optimise WWTP flow measurement for process efficiency
In wastewater treatment plants, the right flow measurement instrumentation ensures optimal...
Precise flow measurement for ultra-pure water
Anton Paar's single straight tube L-Cor Coriolis mass flowmeters offer a reliable and...