Connect your pressure measurement to the future
By Philipp Michel, Product Manager for level and pressure, Endress+Hauser Schweiz AG
Monday, 01 August, 2022
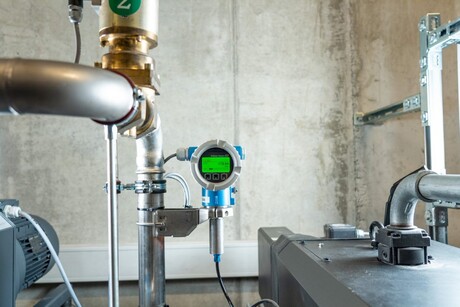
If you compare the change of a plant in the chemical industry over the last few years, you will quickly notice that the number of devices in safety-critical areas has grown significantly. The requirements of the sensors installed in such a facility are also constantly increasing. With all the increasing safety, however, the human-machine interface must not be neglected. What good is a safe sensor if it can only be put into operation by experts?
In order to meet all these requirements, Endress+Hauser has launched a new generation of the well-known Deltabar and Cerabar family.
Improve process safety with a smart approach
Making instruments ‘SIL ex-factory’ is one of the aims of IEC61508. By complying with this international standard, measuring devices can be used in SIL applications as soon as they are introduced to the market — even in a SIL 3 application with homogeneous redundancy. With the implementation of IEC61508, manufacturers of measuring devices ensure the elimination of the intensive operational tests and at the same time reduce any form of systematic errors to a minimum.
But one sensor alone is never responsible for all errors in the process. A large number of errors are also caused by incorrect or faulty commissioning or changes after commissioning. To counteract these errors, Endress+Hauser’s latest pressure measurement line is equipped with guided operating sequences. They guide the user step-by-step through the commissioning and the SIL locking of the sensor, and provide the necessary assistance for the SIL proof tests. If the user has been correctly guided through the commissioning sequence, the device will form an automatically generated checksum (CRC). This checksum contains all safety-relevant parameters. Thus, it can be seen at a glance whether or not a parameter was modified after the initial commissioning.
A further feature that speeds up the check-up during operation is the backlight of the display. In the event of an error, it changes from green to red. The color change allows the operator to immediately notice malfunctions without having to open the menu structure of a device.
Increased productivity through digitally optimised processes
Nowadays, users not only have to deal with a large number of measuring instruments, but also with a wide variety of manufacturers. Intuitive operation is therefore an enormous relief in everyday life. With the new Cerabar and Deltabar generation from Endress+Hauser, the user can benefit from intuitive parameterisation. By implementing a Bluetooth interface, devices that were previously difficult to access or in danger zones can now be operated easily and safely.
Despite all the progress made, data security should not be underestimated in today’s world. Endress+Hauser’s Bluetooth communication is based on a special protocol that meets the high security requirements even for industrial use. The Bluetooth protocol was tested by the Fraunhofer Institute AISEC, which put the interface through its paces. At the end of all tests, the protocol and the algorithm were rated with the protection level ‘High’. This means that manipulation attempts during the connection between app and device can be almost completely excluded.
In addition to the operation of the device, the availability of device information is also extremely important. With an electronic nameplate (RFID or QR code) the user has the possibility to display all device-specific information in real time. This includes not only the device documentation, but also product availability and suitable spare parts for the device.
Unlock your IIoT potential
The times are long gone when a new generation of devices offers only improved accuracy, faster processors or new types of communication. The digital innovations focus on one thing in particular: simplifying the user’s daily work.
One way to simplify the user’s work is to provide data-based insights into their process. In return, these insights can be used to optimise production processes. These values are sometimes worth more than the last decimal point of accuracy.
At Endress+Hauser, special transparency is made possible by Heartbeat Technology, which has already been successfully developed into other measuring instruments in recent years. The concept is based on three pillars: Diagnosis, verification and monitoring.
The ‘diagnostic’ element comprises the continuous self-diagnosis function of the pressure transmitters, achieving a diagnostic coverage of more than 95%. If the device detects an irregularity, it informs the operator via the standardised NAMUR status messages and indicates via an extended error code which measures must be taken to restore the device to a working condition.
With the ‘verification’ functionality, the user has the possibility to create a verification protocol without interruption of the production process and thus inform himself about the correct function of the device. This enables the maintenance effort of the next system revision to be determined in advance, saving a considerable amount of time during a planned shutdown.
The Heartbeat Monitoring function detects irregularities in the process. By recording measured variables, such as pressure peaks caused by water and steam hammer, the operator is provided with the necessary database to carry out predictive maintenance for the surrounding plant components. In addition, deviations in loop resistance and blocked impulse lines can be detected at an early stage. All this improves the understanding of the maintenance process considerably and enables precise maintenance planning.
All advantages at a glance
Reliable and secure thanks to:
- development according to IEC 61508
- automatic checksums after SIL locking procedure
- guided sequences for SIL locking and proof tests
Simple operation for the user thanks to:
- intuitive commissioning via Bluetooth interface
- operation by optical keys without opening the housing cover
- HistoROM ensuring easy transfer of parameters
Fit for the future thanks to Heartbeat Technology and:
- verification in installed condition without process interruption
- 24/7 self-diagnosis of the device
- monitoring of parameters for the improvement of process quality
For more information click here.
Reducing emissions from industrial processes by effective particulate monitoring
Continuous particulate monitoring instruments play an important role in air pollution control.
How to optimise WWTP flow measurement for process efficiency
In wastewater treatment plants, the right flow measurement instrumentation ensures optimal...
Precise flow measurement for ultra-pure water
Anton Paar's single straight tube L-Cor Coriolis mass flowmeters offer a reliable and...