Quality control of veneer strips with a laser triangulation sensor
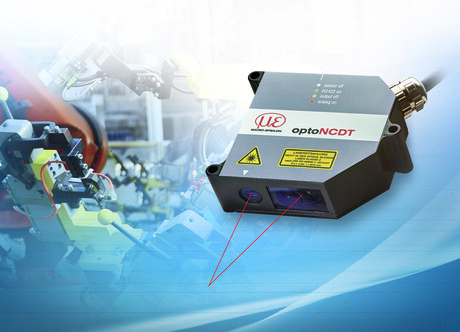
Veneer strips are thin sheets of wood of about 1 mm thickness or less that are manufactured by cutting laminated woods with cutter disks. They are generally used to produce flat panels such as doors, tops, and panels. The strips can also be further utilised for assembling parts of furniture, cabinets, and drawers. These sheets are obtained by slicing large rectangular blocks of wood or peeling the trunk of a tree. Thereafter, they are glued together to form layers over a thick core. After this transformation, they become highly stable and less prone to splitting and cracking than solid wood.
The finished products should be thoroughly checked to make sure the thickness of the strips does not exceed 1 mm as per industry specifications. They can only tolerate marginal error in the micrometre range. Furthermore, they are checked for any inconsistent thickness or splinters that can cause the furniture to delaminate or peel back at edges. Therefore, reliable sensing and detection technology must accurately measure the sheets’ dimensions to ensure that they meet the production standards.
Laser triangulation as a solution
Offering fast, wear-free measurement capability with precision, a laser triangulation sensor is widely used for measuring thickness and dimensions in industrial applications. Laser sensors have a compact design that allows easy integration into industrial machinery. The sensors can therefore be installed into cutter disks easily.
The optoNCDT 2300 laser triangulation sensor from Micro-Epsilon is used in the post-processing stage to check the quality and dimensions of wood veneer. This depends on the precision of the cutting disk used for slicing the laminated wood. The laser is positioned in such a way to measure and monitor the radial deviation of the cutting disks. The cutting disk is fitted with 24 blades, has a 3200 mm diameter, and rotates at approximately 180 to 210 rpm.
The optoNCDT 2300 laser displacement sensor is capable of generating constant and reliable measurement results under challenging conditions. This is due to its ability to offer high-speed measurements and perform reliably with changing and challenging surfaces. The optoNCDT2300 sensor has the feature to rapidly compensate for changing surface during continuous exposure in real-time, which means sudden change of surface will not show erroneous data.
The laser sensor comes with a protective housing to protect the laser from shadows that can impair the measurement. As a result, the formation of dust and wood chips also has a negligible effect on the measurement accuracy. The strongly reflecting surface of the cutting disk and the high-speed operation also doesn’t affect the measurement process. This is because the sensor is integrated with a high-performing optical system to generate precise measurements under rough and challenging conditions.
The sensor can also be connected to a PC via a serial interface. This enables measurement to directly transfer results to the connected PC to post-process the measured values and signals. The intuitive, easy-to-operate web interface allows the users to configure and set pre-measurement settings easily.
The optoNCDT 2300 laser triangulation sensor exhibits high resolution and fast-measuring capability. It is suitable for this type of measurement application as it can offer precise measurement with a sub-micrometre resolution. It can also measure at a speed of up to 49 kHz to suit dynamic applications.
ANS/ANM58 PROFINET: The absolute encoder generation for higher productivity
SICK has launched the ANS/ANM58 PROFINET, an absolute encoder generation specifically designed to...
The future of automation: Siemens SIMATIC S7-1200 G2
Industrial automation has entered a new era: one that demands smarter, faster, and more connected...
New laser scanner series with LiDAR technology for contour measurement and navigation
The latest laser scanners from Leuze are engineered to ensure manufacturing and logistics...