Octobot demonstrates autonomous soft robotics
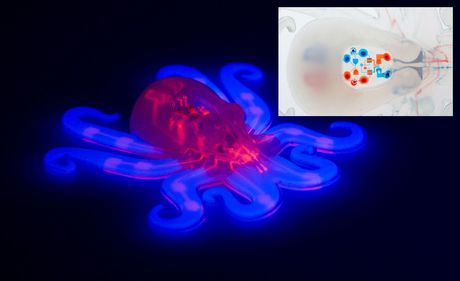
A self-powered, octopus-inspired, entirely soft robot has been demonstrated in Nature. Soft robots are resilient and have the ability to adapt to some natural environments better than conventional robots made of rigid materials.
The new soft robot has eight arms that are pneumatically driven by the release of oxygen gas from a hydrogen peroxide fuel source reacting with carefully placed platinum catalysts, Jennifer Lewis and colleagues have reported. They created the so-called ‘octobot’ using a combination of methods, including 3D printing of the pneumatic networks within the soft body. The octobot operates for between four and eight minutes, a run-time that could be improved by a more sophisticated design of the components that control how the fuel is used, the authors suggest.
Soft robots possess many attributes that are difficult, if not impossible, to achieve with conventional robots composed of rigid materials. Yet, despite recent advances, soft robots must still be tethered to hard robotic control systems and power sources. New strategies for creating completely soft robots, including soft analogues of these crucial components, are needed to realise their full potential.
According to the report, “Soft robotics is a nascent field that aims to provide safer, more robust robots that interact with humans and adapt to natural environments better than do their rigid counterparts.”
The report goes on to say that unlike conventional robots composed of rigid materials, soft robots based on hydrogels, electroactive polymers, granular media and elastomers are physically resilient and have the ability to passively adapt to their environment. Moulded and laminated elastomers with embedded pneumatic networks are widely used materials in soft robotics. Actuation of these elastomeric composites occurs when interconnected channels that make up the pneumatic network are inflated with incompressible fluids or gases supplied via tethered pressure sources. Robotic end effectors with bioinspired and rapid actuation, deployable crawlers, and swimmers with complex body motions, as well as robust jumpers, have been developed on the basis of this design strategy. However, in each case these robots are either tethered to or carry rigid systems for power and control, yielding hybrid soft–rigid systems.
The octobot is an example of the untethered operation of a robot composed solely of soft materials.
The robot is controlled with microfluidic logic that autonomously regulates fluid flow and, hence, catalytic decomposition of an onboard monopropellant fuel supply. Gas generated from the fuel decomposition inflates fluidic networks downstream of the reaction sites, resulting in actuation. The body and microfluidic logic of the robot are fabricated using moulding and soft lithography, respectively, and the pneumatic actuator networks, onboard fuel reservoirs and catalytic reaction chambers needed for movement are patterned within the body via a multimaterial, embedded 3D printing technique.
The researchers conclude that the new design and fabrication approach lays the foundation for a new generation of completely soft autonomous robots that are able to perform more complex functions.
Excelitas pco.horizon 9.1 bi TDI CLHS Line Scan Camera
The pco.horizon 9.1 bi TDI CLHS Line Scan Camera is designed for precise inspection applications...
ABB IRB 6730S, IRB 6750S and IRB 6760 large robots
ABB Robotics is expanding its large robot range with the launch of the IRB 6730S, IRB 6750S and...
ABB IRB 1200 industrial robots
ABB Robotics is releasing a new generation of its IRB 1200 small robot range that it says is...