Fully automated QA for electrical switch manufacturer
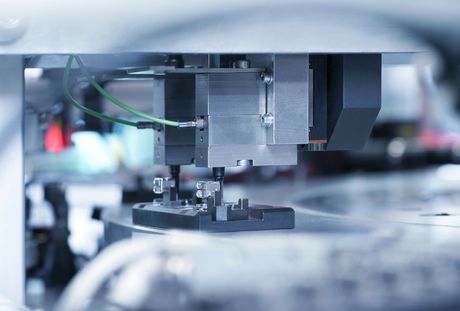
The market that switch and socket manufacturer Feller supplies is extremely dynamic and places highly stringent demands on both management and production. Since quality plays such a fundamental role for the Horgen-based maker of electrical goods, manufacturing is carried out wholly on-site in Switzerland.
At first glance, it may seem that Feller would benefit from the lower production costs achieved by manufacturing in a low-wage country, but the pitfalls would be considerable. The company could run the very real risk of producing unchecked, defective parts such measures which ultimately paralyse an entire installation for months on end. Feller’s objective, therefore, is to establish real-time, zero-defect production locally and thereby achieve sustainable optimisation.
Peter Suter is group manager for automation at Feller and is responsible for ensuring trouble-free production. He confirms that zero-defect production is a fundamental criterion for market success today in the field of electrical installation.
“The requirements for quality are continuously increasing. Over the years, tolerances for acceptable waste have become more and more stringent — something that is also reflected in the requirements for continuous process improvement and associated quality tests. As a result, it is not surprising that the aim of the fully automated process at Feller is the final testing of each individual product,” he says.
In 2008, new standards for switches and sockets in the Swiss energy market presented new challenges for Feller. Based on these new stipulations, a completely novel production line was implemented in the plant.
“One requirement for the new production line was to guarantee quality standards using force/displacement monitoring. This was part of the design specification presented to the mechanical engineer. To monitor the caulking at the rocker switch, Insys from Münsingen proposed using Kistler technology. The new production line — equipped with Kistler sensors — was commissioned in 2008,” said Suter.
In 2011, the continuous increase in quality requirements resulted in the need to check the switch functionality when it was installed (in addition to the caulking of the rocker switch).
“In this context, the switching point of the switch is tested again in a further step. The aim here is to ensure that any switches that are not 100% in order do not generate further costs. All switches that do not meet the desired functionality, or require excessive effort to switch over, are removed from the process directly in the course of this test,” explained Suter.
The solution for this second application was developed specially by Feller. As the company was satisfied with the force/displacement monitoring solution from Kistler, it was clear that the company’s technology should be adopted to perform this testing. Feller therefore discussed solutions with the Kistler team and subsequently implemented a low-force sensor.
“Due to the low forces and confined space, our solution implemented Kistler’s Type 9215 sensor. Thanks to the optimal installation and the minimised design, this solution delivers a high force resolution today. Installation of Kistler’s low-force sensors provides a closed system that supplies reproducible, reliable values and brings quality assurance to a completely new level,” he said.
“For the initial delivery, Kistler was recommended to us by our machine suppliers — and thanks to the company’s good reputation in the industry, we did not question this. In the case of the second requirement, which Feller retrofitted into our existing plant, the positive experience from that first application meant that Kistler was the only company we considered for the job.”
For Feller, this has paid off 100%. “Our production is highly efficient and delivers verified, 100% defect-free parts today,” said Suter.
Excelitas pco.horizon 9.1 bi TDI CLHS Line Scan Camera
The pco.horizon 9.1 bi TDI CLHS Line Scan Camera is designed for precise inspection applications...
ABB IRB 6730S, IRB 6750S and IRB 6760 large robots
ABB Robotics is expanding its large robot range with the launch of the IRB 6730S, IRB 6750S and...
ABB IRB 1200 industrial robots
ABB Robotics is releasing a new generation of its IRB 1200 small robot range that it says is...