Conveying in the third dimension: RFID beats barcode
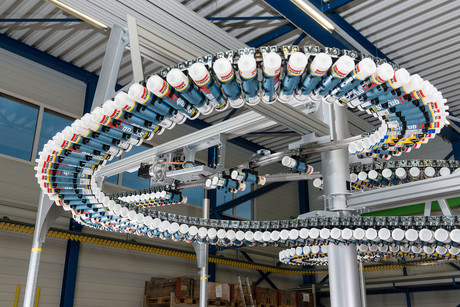
Barcodes are a cost-effective and versatile solution when goods need to be marked and unambiguously identified, but this optical detection method soon encounters its limits when the labels become dirty or damaged during the process and can then be hardly read, or not read at all.
Ferag AG, headquartered in Hinwil, Switzerland, has therefore opted to use RFID technology in the conveying technology that it has developed for various industrial applications and material distribution systems.
Its innovative conveying system, known as Skyfall, is a system that makes intelligent use of gravity and moves free-fall sections without its own drive. This saves energy and reduces the number of drives required. Thanks to a line layout with distance radii of 500 mm and generous tilt angles of up to 6° the system requires relatively little area, so there is also comparatively more room on the plant floor for free spaces and filling and packaging equipment. The innovative conveying system is multitalented. In intralogistics it overcomes longer travel distances and height differences, connects or uncouples workstations and integrates filling, picking and packaging functions at the same time.
A recent example is a filling and packaging process for tubes of construction silicone, in which the system had to meets a special requirement of the user: eliminating the previous bottleneck between the filling station and batch packers. This is achieved because Skyfall not only handles transport of the cartridges but also the accumulation buffer. “In this way,” said Roberto Fenile, development manager at Ferag, “the differing speeds of the filling and packaging process can be compensated for and a consistently high system output is achieved. Compared with the previous approach, we have been able to double the production capacity.”
The conveyor system has an output of 12,000 cartridges per hour and runs so smoothly that an observer can hardly follow the cartridges as they move past. The heart of the overhead design is a rugged rail system with three-dimensional kinetics and roller bodies, called shuttles. These are loaded with the construction silicone cartridges which differ not only externally but also in their volumes. The empty cartridges are brought from a storage bunker to be filled at the end of the conveying and sorting process with specific amounts of construction silicone, then brought to a batch packer. Reliable identification of each individual shuttle is absolutely critical for the process, which is why Ferag decided on an RFID-based identification method.
“It even works reliably when the data carriers are contaminated by silicone residue,” said Rolf Werner, Balluff sales engineer.
The transport approach embodied in Skyfall is not limited to the cartridges, because shuttle adapters allow them to be individually configured and adapted to the respective application. In addition, the modular system can always be expanded as needed with available standard elements such as continuous conveyors, ascending and descending conveyors, loading and unloading stations, or inlet and outlet transfer gates and adapted to new situations.
Ferag chose the BIS M industrial RFID solution from Balluff, which operates at a frequency of 13.56 MHz. “It not only meets the demanding requirements with respect to cycle rate and ruggedness, it can also work reliably in challenging metallic surroundings,” Werner explained. Combined with passive data carriers, this HF solution offers average ranges of 20 mm. This makes BIS M suitable for parts tracking at close range or applications in production control or tracing for quality management. At Ferag, the system not only enables uninterrupted documentation of the processes but also provides the data to the controller in real time and automates the complete material flow, including the filling and packaging process. The type and current location of each individual cartridge is known during the entire process. Data management is performed in the system’s central computer.
Self-adhesive OnMetal RFID tags just 36 x 8 x 5 mm — similar to a part label — enable very flat identification of the shuttle. Since the data carriers bear a serial number fixed in memory (the so-called UID code), the shuttles can be identified unambiguously at any time. The data carriers conform to the international ISO standard 15693 and provide a general read distance of 10 mm, even on metallic substrates. This was one of the essential requirements of Ferag. Uninterrupted detection of the roller bodies is thus ensured over the entire material flow.
The UID is read by tubular M16 read/write heads from the Balluff RFID system, which are located at all the relevant locations along the transport path, such as at gates. The data carriers are passive, receiving the needed power from the read/write heads. This makes batteries unnecessary — the electronics and antenna are integrated into the tag.
“The great art is selecting the right system and the optimal combination of tag, read head and controller. We got expert support in the selection from the Swiss Balluff technical support in the person of Willi Brändli,” said Fenile. “Mr Brändli was immensely helpful and also worked hard to assist us with the implementation.”
“The size of the data carrier and the geometry of the read/write head play an important role,” explained Brändli. “The HF field generated in the application must be large enough so that the tag dwells in the field long enough for us to read out the identity even at high speed. But at the same time, it needs to be small enough that there is no overlap with the following label during the detection process. This requires a lot of experience.”
“At first we tried the solution from another RFID provider, but under these complex requirements it didn’t work,” said Fenile. “Then we compared the systems from different manufacturers and finally decided on Balluff, because as a developer and manufacturer this company knows its products backwards and forwards yet doesn’t shy away from going beyond the standard products to develop customer-specific variants.” Happily, however, this solution was able to be achieved using standard components from the Balluff line.
With the BIS V RFID controller an all-in-one unit is built into the system, which allows connection of up to four read/write heads. Combined with the read heads, it offers the required high-read speed. Due to the four ports the number of controllers required is reduced, saving Ferag considerable expense. If necessary, read heads using different technologies (LF, HF and UHF) can be connected.
Start-up of the RFID system and handling of the controller is plug and play. The read/write heads are simply connected to the front of the controller, after which they are immediately and automatically detected. Two LEDs on each port indicate their status and operating condition. Since the controller supports the use of standardised frequencies, it can be used anywhere in the world the Ferag system finds itself. In addition, the combi-controller in the compact metal enclosure is available for all common bus systems (Profibus, EtherCAT, CC-Link, EtherNet/IP and Profinet). In this system, Ferag uses EtherCAT.
A USB terminal on the controller serves as a service interface, such as for software updates and for fast start-up, with no need for a PLC or controller. The ‘intelligent’ combi-controller also allows additional sensors or actuators to be connected to the RFID processor unit using built-in IO-Link master functionality. This makes it possible to not only identify objects but also to obtain additional process information via the controller, such as signals from trigger light barriers, from inductive or capacitive proximity switches or from distance or vision sensors with an IO-Link interface. Even if there is no initial requirement for such functionality, the system is well-equipped for any future requirements.
Phone: 03 9720 4100
Excelitas pco.horizon 9.1 bi TDI CLHS Line Scan Camera
The pco.horizon 9.1 bi TDI CLHS Line Scan Camera is designed for precise inspection applications...
ABB IRB 6730S, IRB 6750S and IRB 6760 large robots
ABB Robotics is expanding its large robot range with the launch of the IRB 6730S, IRB 6750S and...
ABB IRB 1200 industrial robots
ABB Robotics is releasing a new generation of its IRB 1200 small robot range that it says is...