NZ expertise shines in new beverage processing plant
Monday, 30 January, 2017 | Supplied by: Thermaflo
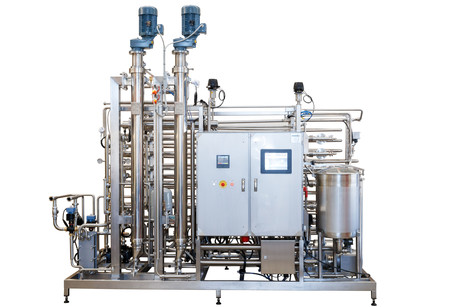
As the global demand for new and innovative beverages is entering a new age of lower sugar, greater convenience and higher value we are beginning to see more and more companies pushing the boundaries of what was once considered traditional beverage production techniques.
In early 2015 Australian-based Multipack, a contract beverage processing and packaging company, wanted a new beverage processing plant to produce a new coffee creamer for a major US manufacturer along with various other products. Multipack contacted Thermaflo for the design, fabrication, installation, automation and commissioning of a multipurpose beverage processing plant.
The plant was designed to process a wide range of beverages of various viscosities with up to 75% solids. To ensure the system ran smoothly and could handle the demanding duties, Thermaflo staff spent a lot of time developing the design. Once the design had been finalised the system consisted of two scraped surface heat exchangers, two tubular heat exchangers and three different sets of holding tubes which were all controlled by a PLC and HMI touch screen. This allowed for flexibility in the process as the various recipes and parameters were saved within the PLC.
At the beginning of the process, product is transferred via a progressive cavity pump from the product mix tank through to the pasteuriser’s balance tank where it is level controlled. From the balance tank, product is then pumped through the tubular heat exchanger for preheating, utilising an onboard electric hot water system.
From the preheater, product is transferred to a scraped surface heat exchanger, where the product is heated further to achieve the heating setpoint. Following heating the product is transferred through a set of holding tubes. The length of the holding tube can be set prior to starting production — this is achieved by connecting the appropriate pipework to adjust the holding tube length, which in turn sets the holding time (the time it takes product at the set flowrate to traverse the holding tube).
Once the product has progressed through the holding tubes, the temperature is recorded before reaching a divert valve. If the desired product temperature is not met the product will be diverted back to the pasteuriser balance tank for further processing via the automated diversion system. When the product temperature setpoint is reached the divert valve will automatically change the product flow forward again for further processing.
After the holding tubes the ‘heat treated’ product is cooled via two cooling sections; the cooling system consists of a tubular pre-cooler heat exchanger that utilises a closed cold water loop running at 20°C. This pre-cools the product down approximately 20°C. From there product is transferred to a scraped surface heat exchanger where it is further cooled to achieve the cooling temperature setpoint using 7°C chilled water.
After the cooling section the product is sent to a pasteurised product tank where it remains until it is forwarded to a filler for bottling and packaging.
The system is all mounted on a stainless steel skid frame, which allowed for a much simpler installation once the skid arrived on-site. This also allowed Thermaflo to set the plant up in its workshop in Palmerston North, New Zealand, to carry out the pre-commission prior to shipping.
This project has definitely been a one of a kind that has surpassed both Thermaflo’s and the client’s expectations.
Originally published here.
Phone: 0011 646 353 3640
Pfannenberg PROTECT Series signalling solutions
With a strong die-cast aluminium housing, the PROTECT series is designed to withstand harsh...
EXAIR ATEX cabinet cooler systems
EXAIR's ATEX Cabinet Cooler systems are designed to provide a solution for keeping electrical...
DEWESoft GridPhase phase identification system
GridPhase is a phase identification system designed to bring precision and efficiency to phase...