Positioning systems improve airport logistics
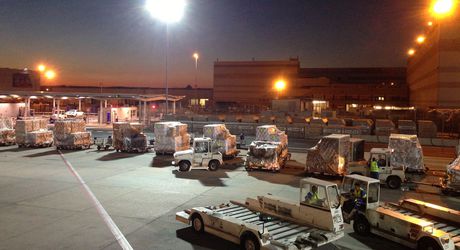
An airport apron bustles with traffic — the tow tractors, tankers and buses moving busily around a jet run the risk of colliding. An enhanced positioning system will increase safety and the efficiency of logistical operations in the future — and available airport capacity will be utilised better.
Dense fog is hanging over an airport apron. Even when tow tractors, pushback tractors and tankers are moving at merely a snail’s pace, collisions can always occur, be they with other vehicles or with aircraft. Tanking and loading of luggage, air cargo and catering takes significantly longer in fog or rain than when visibility is clear. Passengers end up sitting at departure gates longer than planned, and the schedule for cargo containers is jeopardised too.
Poor weather conditions will impede work on the apron far less in the future. Researchers at the Fraunhofer Institute for Factory Operation and Automation IFF in Magdeburg are establishing the basis for this in the EU project ‘e-Airport’, together with various European partners.
“We are developing a positioning system that will increase safety on the apron,” explains Olaf Poenicke, research manager at the Fraunhofer IFF. “It will additionally make it possible to utilise airport capacities more efficiently, because the system allows logistical operations to run in a significantly more structured way than before.”
One important aspect: the steady increase of air traffic is compelling airports either to build new runways and terminals or to utilise the existing infrastructure’s capacities more efficiently.
The European Galileo satellite system is the basis of the novel positioning system in the e-Airport project. The principle is similar to that of an automotive navigation system: tow tractors, pushback tractors and other vehicles have onboard receivers for global navigation satellite systems (GNSS). They receive signals from the Galileo satellites and other systems such as GPS and use them to establish their exact location. Positioning data are sent by WLAN or cellular radio, for instance, to the control centre. The control system, in turn, sends messages back to the drivers: a display warns when a vehicle is getting too close to another, driving too close to restricted areas or leaving a specified route.
“We at the Fraunhofer IFF are contributing our expertise in air cargo to this control centre, modelling the processes and specifying the job orders received by a tow tractor driver,” explains Poenicke.
The process models help define ideal target processes. They are compared in the control centre with actual data sent from the apron by sensors. Discrepancies can thus be identified, and instructions derived from them can be sent to tow tractor drivers.
Although positioning systems that determine vehicle locations exist, they are based on GPS. This entails problems, especially in the vicinity of buildings. Shadowing occurs; positioning data are imprecise or break off completely. This doesn’t happen in e-Airport: additional signals from the Galileo satellites and other correction signals from the European EGNOS D-GPS system increase accuracy and reliability substantially.
Up to now, tow tractor drivers have usually received printed work assignments. Where do they have to hitch which dollies (trailers loaded with air cargo pallets or containers)? Where should they deliver them? Errors occur time and again. Dollies are parked on the airport premises and forgotten, for instance, and have to be hunted laboriously later. “Our system eliminates such errors. It knows both the desired and actual status and gives the driver pertinent work instructions,” says Poenicke.
The researchers are additionally developing special wireless sensors which are attached to dollies. They use an energy-saving wireless protocol to send their data (a trailer’s identification number and load) to a receiver unit in the tow tractor. The unit automatically analyses which dollies are hitched and relays the dolly data, together with the tow tractor’s positioning data, to the control centre. The latest status data keeps the e-Airport system always in the know, even about the location of a dolly parked on the apron. In short, the control centre has aggregated data not only on vehicles, but also on their dollies and the cargo loaded on them.
Mettler Toledo oxygen measurement guide
Mettler Toledo has produced a guide for the process industries that explains the measurement...
Mettler Toledo pH sensors operating guide
Mettler Toledo has released a booklet describing good operating procedures for pH sensors, aimed...
Honeywell Process Solutions LEAP project services
Honeywell Process Solutions has launched its LEAP project services (Lean Automation of Automation...