Increasing safety in waste sorting plants
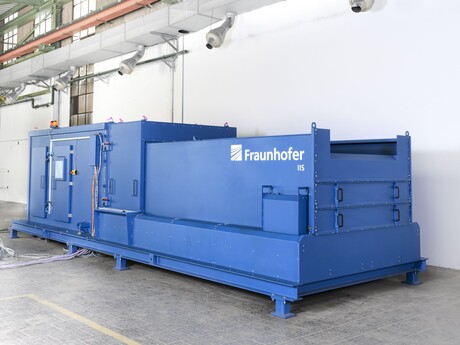
An increasing amount of electronic waste is not being properly disposed of, instead being discarded together with other waste. If the batteries in these products are damaged, they can cause fires at sorting plants. As part of the DangerSort project, researchers at the Fraunhofer Institute for Integrated Circuits IIS are using a sensor-based sorting system to remove hazardous items and make recycling plants safer.
More than 10,000 fires occur annually in German waste sorting plants, and around 80% of these fires are caused by lithium-ion batteries. Common in smartphones, electric toothbrushes and even singing greeting cards, these batteries are often disposed of together with packaging waste. They can be damaged and catch fire, particularly during the recycling process in sorting plants. The damage caused by this is estimated at around one billion euros a year.
The DangerSort project aims to reduce the risk of fire in sorting plants.
“We are developing a sensor-based sorting system that uses X-ray technology and artificial intelligence to detect hazardous lithium-ion batteries and separate them from the rest of the waste stream at an early stage,” said Johannes Leisner, Head of the Sorting and Laboratory Systems group at the Development Center X-ray Technology at Fraunhofer IIS. “So far, there have been no preventive measures against fires caused by batteries — only solutions to combat them, such as improved fire extinguishing systems. The sensor-based technology could also make it easier to recycle batteries, closing their product life cycle.”
A prototype system set up at Fraunhofer IIS demonstrates the potential of the idea. A high-speed conveyor belt in the X-ray sorting system, which moves at speeds up to 3 m/s, transports the waste stream. An X-ray source above the conveyor belt operates like an airport luggage scanner and screens the material stream. This technology can also identify batteries installed in appliances or concealed by other waste. An X-ray detector mounted below the conveyor belt takes images at the speed of the conveyor, resulting in a continuous series of radiographs. The series of images is then evaluated.
“To do this, we are applying an AI system that is designed for particularly rapid image processing and is normally used in autonomous driving applications,” Leisner said. “We have adapted and retrained it so that it can also analyse radiographs to specifically detect electrical appliances that contain lithium-ion batteries.”
Sorting is initiated based on the data collected. This information enables the control of compressed air valves that separate hazardous electrical appliances from the waste stream. Air nozzles measuring around 5 mm remove them from the belt and convey them into a separate chamber. The right timing between evaluating the radiograph and starting the nozzles is crucial for this process.
“It is difficult to detect and isolate different battery sizes during the separation process, as these can range from 10 kg e-bike batteries to button batteries,” Leisner said.
At the time of writing, the sorting system is still undergoing tests at Fraunhofer IIS; the plant is scheduled to be delivered to waste disposal company LOBBE in early June for the first practical tests. The project, which is funded by the German Federal Ministry of Education and Research (BMBF), will run until the end of August 2025.
Mettler Toledo oxygen measurement guide
Mettler Toledo has produced a guide for the process industries that explains the measurement...
Mettler Toledo pH sensors operating guide
Mettler Toledo has released a booklet describing good operating procedures for pH sensors, aimed...
Honeywell Process Solutions LEAP project services
Honeywell Process Solutions has launched its LEAP project services (Lean Automation of Automation...