Taking the pain out of plant maintenance
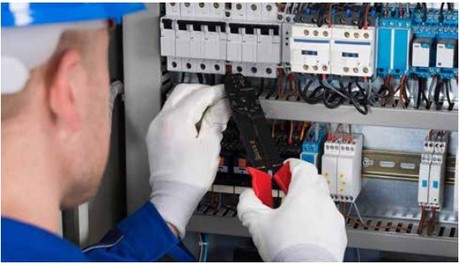
Careful planning and close collaboration with suppliers are key elements in achieving effective plant maintenance, according to a leading UK industrial laundry firm. Berendsen UK Ltd, part of the Elis S.A. group, an international provider of textile, hygiene and facilities services across Europe and Latin America, outlines why this approach provides the building blocks for effective plant maintenance.
Plant maintenance is always an area of business that needs to be handled carefully.
“While you have to factor in a certain amount of planned and unplanned maintenance, the aim is always to have your machines working as close to 100% of the time as you can,” explained Barry Quinn, Engineering Manager at Berendsen. “A good plant maintenance strategy is essential for us — any downtime has a direct impact on the bottom line, so you need to be set up so that both planned and unplanned maintenance has as little impact to your daily operations as possible.”
Be prepared
Planned maintenance, as the name suggests, comes down to organisation, according to Barry.
“You need to firstly identify the best time to do the work and where it will have least impact on your productivity,” he said. “Then you need to make sure that you will have the parts required — we work with RS who ensure we have everything we need, when we need it.”
Look to collaborate
Collaboration between a business and its suppliers is crucial when it comes to effective plant maintenance.
“We look at RS and our other suppliers as partners,” said Barry. “We work together to make sure that our machines are always online. We rely on RS’ knowledge to make everything run smoothly.”
Grace Skewis, RS representative adds: “We need to work with the customer as part of a team. I spend time with my customers and get to know their business so that I can give them advice that benefits them. For example, if a customer orders a certain part once every six months, this could be a low usage item but a critical spare. We would keep two in stock and only re-order when one is used — this ensures that we have a spare part at all times in the event of an emergency and re-stock only as required.
“It may sound simple, but it’s these sort of steps that avoid unnecessary downtime.”
Identify the right solutions
It’s clear to see that the best approach for modern maintenance is a combination of planned and preventative measures, avoiding reactive maintenance whenever possible.
There is a plethora of solutions available to help in this area: from handheld test and measure equipment that can be used by operatives to monitor variables such as pressure and temperature, to sensing products that monitor machine condition and alert operatives to potential issues. When it comes to smart solutions, the latest sensors allow integration with connected machines, with cloud computing platforms providing data to determine the health of the machine, enabling prediction of potential points of failure for breakdown. IoT will fast become the main element in the creation of an effective predictive maintenance strategy.
Making intelligent product selections can also help avoid breakdowns. Choosing to fit long-life bearings helps negate downtime, while ensuring you have the right lubrication is vital to obtaining the best operational life from mechanical systems. Investing in more advanced test and measurement such as motor analysers, thermal imagers and vibration analysers can help uncover unseen component degradation prior to the point of failure.
Keeping abreast of technology evolution and solutions, planning how best to structure and deploy maintenance teams, and ensuring the right parts are available when required are all critical to an effective maintenance strategy.
Working with a knowledgeable distributor such as RS, which offers guidance material online and works closely with leading brand specialists to advise on specific applications, will be invaluable for accessing the right products and knowledge to optimise a maintenance program.
Do you have any questions about our products, services or delivery options? Visit our website.
In a digital world, why is value still hard to find?
At all levels of an industrial system there are a number of barriers that make it difficult to...
Machine learning in manufacturing process control: How ARDI enhances operational efficiency
With increasing data availability, machine learning has become a powerful tool in the...
Verifying and Validating AI in Safety-Critical Systems
In the era of AI-enabled safety-critical systems, validation and verification is becoming crucial...