Fluid processes without danger
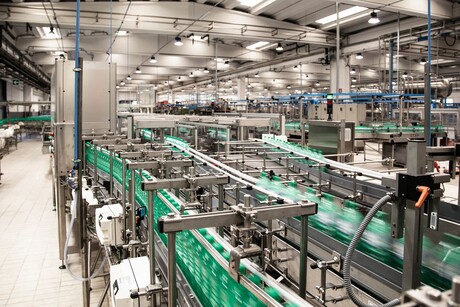
Design and automate a plant for filling and packaging 44,000 square PET bottles per hour for the largest Italian bottler of mineral water?
ACMI S.p.A. was faced with this task and developed a plant comprising interlinked machines. The entire process should be productive and three appropriately trained users should be able to control it. Pilz took on the risk assessment and developed the necessary safety measures to ensure safe interaction of the machines. The result is a safe, productive packaging process.
Complex filling and packaging machinery under control
There are many individual steps behind the bottling of mineral water, and therefore many plant components, from the blow-moulding/filler block that blow-moulds, fills and seals PET bottles, a complex design of conveyors conveys bottles to control and labelling stations, and finally to the packaging machines and palletisers.
Risk assessment for packaging machines
To determine which risks are possible when operating the plant and which protective measures are necessary, ACMI — a manufacturer of complete end-of-line systems and packaging machinery — consulted with its long-standing partner Pilz. The task was to conduct a risk evaluation of the individual parts of the plant in accordance with the applicable standards and regulations, including the packing and handling machine, the palletiser and the two different wrappers and depositors. The interfaces between these machines and parts of the line not coming from ACMI were also examined. Pilz identified and documented the risks in the lifecycle of the machinery in order to determine the limits of the linked line.
Finally, the automation experts used this as a basis for conducting a risk assessment in order to draft the optimum strategies and measures for risk mitigation.
In a further step, performed on a second visit, Pilz validated the protective measures implemented, which allowed the RESS (Requisiti Essenziali per la Salute e la Sicurezza — basic health and safety requirements) for reducing the risk of accidents. In Italy, the RESS describes the national, basic health and safety requirements that are part of the European Machinery Directive 2006/42/CE. Pilz also produced the technical documentation and the operating and maintenance manual for the entire production system.
“The risk assessment performed by Pilz experts formed the basis for the safe construction of our plant as well as for the identification of suitable protective measures,” said Gianluca Contesso, Safety Product Manager at ACMI S.p.A. “Pilz’s expertise in machinery safety enabled us to then implement the required measures ourselves.”
The right solution for maximum flexibility
At the heart of the system was safe control technology. The safety functions in the ACMI line are now monitored by the configurable small controller, PNOZmulti 2. The PSENcode non-contact safety switches installed on the safety gates of the line also meet the highest safety requirements up to PL e and SIL 3 in conformity with EN ISO 13849-1 and EN IEC 62061.
PSENcode devices monitor the location of guards and perform general position monitoring. Based on RFID transponder technology, the coded safety switches offer both maximum manipulation protection as well as compliance with minimum spacing requirements. In the ‘unique, fully coded’ version — based on the key-and-lock principle — PSENcode guarantees maximum flexibility and user-friendliness while at the same time being easy to install in accordance with EN ISO 14119:2013.
PNOZmulti 2 also offers the option of expanding the safety logic afterwards and controlling other safety functions such as speed monitoring. This solution allows for intuitive operation and the flexibility that ACMI needs. The possibility of connecting the PNOZmulti 2 to the machine’s existing automation system was made possible by the PNOZ m ES Profinet fieldbus, which can be used to communicate the status of the safety devices. This enables fast and simple identification of any problems that may exist, ensuring high productivity from the individual parts of the machine.
It only takes a few clicks in the PNOZmulti Configurator software tool to adapt to other standard PLC controllers as well, which allows both ACMI and the end customer to remain flexible.
Solution benefits
- Pilz supports its customers with its many years of expertise in every aspect of risk assessment
- Creation of an individual safety concept according to the current status of the standards, taking into consideration productivity
- PNOZmulti 2 and PSENcode can be seamlessly integrated into virtually all existing automation solutions
Our products in application
PNOZmulti 2 PNOZmulti 2 controllers are the second generation of these small controllers with 22.5 mm base units and many extensions for expansion. |
![]() |
PSENcode PSENcode coded safety switches are used to monitor the position of guards and for general position monitoring. Thanks to the integrated evaluation, applications up to PL e and SIL CL 3 are possible with just one switch. |
![]() |
High Integrity Pressure Protection System (HIPPS) 2oo3 voting shutdown system
The Moore Industries SLA Multiloop and Multifunctional Logic Solver plays a pivotal role in...
Navigating SIF logic solver selection: Why the Moore Industries SLA stands out
It is important to select a logic solver that is not just well-documented but fully compliant...
Selecting instrumentation for functional safety (SIL) applications
Over the past couple of decades, the process industries have seen many changes when it comes to...