Power plant control systems upgrade delivers multiple benefits
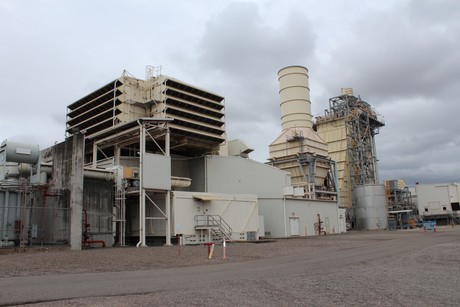
Turbine, plant control and safety systems at two critical gas-fired peak load power generation plants have been modernised to significantly improve lifecycle and risk management.
Ratch Australia owns a 230 MW gas-fired power plant in Townsville that supplies electricity to some 300,000 households, and another 300 MW plant at Kemerton in WA that supplies around 250,000 households.
Strict power price agreements place onus on the electricity generator to provide power when required and significant penalties apply if this is not the case. Ratch decided that a higher level of certainty and flexibility was required in its control platform, so Emerson Automation Solutions was contracted to deliver a new Ovation distributed control system (DCS) and safety instrumented system (SIS) for both the Kemerton and Townsville power stations.
Emerson’s Martin Kolos says Ovation has a significant global footprint in all generation types, including fossil fuel thermal, nuclear, biomass, hydro, solar (photovoltaic and concentration) and wind.
“We took the control and safety logic from the existing systems (a mix of Simadyn, Teleperm XP, S95F, and S7 PLC/SCADA), and integrated it all into a single Ovation control system that provides a unified engineering and operations environment for turbine control, balance of plant control and safety protection systems,” he said. “The control logic was migrated on a like-for-like basis which provided the owner with a reduced risk profile in its decision to deviate from the turbine OEM’s control systems.”
Two open cycle gas turbines for peaking power are installed at the Kemerton power station while the Townsville power station has one combined cycle gas turbine, which includes a heat recovery steam generator and associated steam turbine that is sometimes referred to as the ‘Steam Tail’.
Martin says that a key benefit of the Ovation system is that it integrates SIS. “All engineering and operations are carried in the same software environment, which simplifies engineering, testing and commissioning, and also the lifecycle maintenance — which all helps to reduce the total cost of ownership,” he explained.
“In the immediate term, key benefits for operators include a higher level of flexibility in making control and tuning enhancements, and a more intuitive user experience.
“The longer term benefit is expected to be vastly simplified lifecycle management due to only maintaining a single configuration database for both control logic configuration and operator interface. This is an inherent advantage of DCS technology, and Ovation extends this strength in its ability to control all aspects of power generation.”
General Manager Asset Management and Asset Development at Ratch Australia, Tony Polley, says both plants now have centralised control based upon Windows platforms and are fully able to be remotely accessed by mobile devices, which is a huge benefit.
“Productivity is enhanced due to a faster rate of start-up. Also, safety, risk management and the operator interface are all enhanced due to the new state-of-the-art DCS and power conversion equipment,” said Polley. “In addition, ongoing generator compliance with the respective technical rules is demonstrable in real time due to installation of online high-speed monitoring and data recording equipment.
“The biggest challenge was the conversion of every logic and input/output (I/O) from the old system to the Ovation platform — and the factory testing of every I/O — which amounted to some 2,500 at Kemerton and 3,500 at Townsville. The new Ovation system is significantly more powerful than the former TXP system and is a genuine control platform rather than just a turbine control and monitoring system.
“Another major challenge was the reconnection to the grid network and proving to the respective authorities and bodies — such as Western Power, AEMO, Powerlink and Ergon — that the governors and generator performance complied with the technical rules.”
Tony points out that given that the previous systems were no longer supported, and spares were very difficult to source, a single component failure could result in a loss of ability to generate from either power station. “Therefore it is reasonable to assess that the likely payback time for the project will be short, in terms of the overall lifecycle,” he said.
Steve Clark, Manager Operations at TW Power Services — which provides operational and maintenance services for the Ratch-owned Townsville and Kemerton power stations — says the new control system provided by Emerson offers significant improvement over the previous, antiquated control systems used at the power stations.
“Upgrading from a multi-system control arrangement using a myriad of protocols and interfaces for multiple areas of plant to a single integrated Microsoft Windows-based distributed control system allows Townsville power station to operate in a modern efficient manner,” he said.
“Systems which previously required local operation on-site, and out in the field, can now be controlled and monitored from the on-site central control room, or via Microsoft Remote Desktop on practically any internet connected device.
“The previous systems at both Townsville and Kemerton were end-of-life systems with obsolete hardware and with very limited access to spares. With the new Ovation control system there is modern state-of-the-art equipment, with ready access to spare parts from both local and overseas suppliers.”
Steve adds that as part of the controls update, both Townsville and Kemerton have access to several after-sales support options including a 24-hour telephone hotline, remote diagnostics and interfacing, and local Australian-based support as well as specialist engineering support from Singapore, the Philippines, Costa Rica, Poland, India and the USA.
Phone: 03 9721 0200
Anderson Greenwood Type 84 pressure relief valve
The Anderson Greenwood Type 84 pressure relief valve is designed to protect tanks and vessels...
TESCOM AGI BR Series packaged flushing ring solution
The TESCOM AGI BR Series flushing ring is a packaged solution for flushing and bleeding...
Alfa Laval ThinkTop V55 diaphragm valve control unit
Designed for Alfa Laval diaphragm valves, the slim profile of the ThinkTop V55 is designed to...