Investment in next-gen crushing boosts plant safety and efficiency
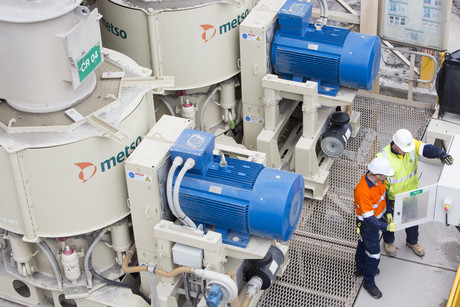
Located in the Adelaide suburb of Seacliff Park, Boral’s Linwood quarry is positioned within one of South Australia’s most important sources of hard rock. Quarrying started here over 130 years ago, when in 1882 the quarry was first operated to supply limestone to the nearby Brighton Cement works. Boral, Australia’s largest building and construction materials supplier, acquired the quarry in 1994. Today Linwood’s operations are focused on providing high-quality aggregate, critical in the production of composite materials such as concrete and asphalt.
Linwood is currently the largest capacity quarry servicing the Adelaide metropolitan area. In recent years, the region has seen a flurry of large construction projects such as Adelaide’s Desalination Plant, the city’s Northern and Southern Expressways and the Royal Adelaide Hospital. As a consequence of these important projects, the demand for aggregate products has progressively increased, challenging the quarry’s production capabilities. In 2013, site management identified the need to upgrade the quarry’s crushing and screening plant with the latest technology in order to meet this growing demand.
Improving primary crusher throughput
The requirement for new equipment first became evident in the quarry’s primary crushing section. The plant’s 30-year-old primary jaw crusher was struggling to keep up with production demands. The machine’s reliability and downtime were affecting overall plant performance. Maintenance costs had risen sharply and the availability of spares had become an ongoing problem. After considering the cost of refurbishing the existing crusher, Linwood’s management decided that investing in a new machine was the best option. Following a detailed analysis of the quarry’s requirements, the team selected Metso’s C140 jaw crusher.
Quarry Manager Andy Baker explains the decision: “Minimising the need to modify our existing civils was a key prerequisite for the new machine. Essentially we needed a modern like-for-like crusher that would fit into the existing footprint, increase throughput and be easy to maintain — Metso’s C140 met all these criteria.”
While improving throughput and reliability was a priority, Linwood’s management also recognised the upgrade as an opportunity to improve site safety. As part of the crusher installation, new walkways and access platforms were designed to improve access to the quarry’s primary crushing station.
Once the C140 was installed, the crusher’s performance and reliability significantly improved product quality and throughput. The new machine’s ability to deliver more consistent output also immediately reduced the load and wear rates in other key areas of the plant. Where personnel previously needed to constantly monitor the crusher to ensure a consistent product output size, this was now an automated process.
“Now we can simply program the gap setting and be confident about what product we are going to get. The C140’s hydraulic adjustment provides a massive advantage for us in terms of overall efficiency and safety. It eliminates manual adjustments and associated hazards. This saves us time and keeps our production rates up,” said Baker.
The plant’s primary crusher upgrade represented a big change for quarry staff, as it brought the latest technology to the primary crushing process in the form of advanced automation and safety. Metso Area Manager Andy Gough said that post-commissioning support was very important to ensure a smooth transition period.
“The new machine offered many benefits; however it was a significant change for the site. We worked hard to maintain a presence at the quarry post commissioning, offering a comprehensive range of support services during this critical period,” he said
A win in tertiary crushing quality and efficiency
Shortly after the new crusher was installed in 2014, its increased production capacity shifted the site’s bottleneck to the tertiary crushing circuit. Tertiary crushing involves further reducing aggregate in size while shaping it into final end products. While it’s important to keep up with upstream feed rates, high precision is required to ensure the right product shape. Linwood had two cone crushers responsible for this task that were nearing the end of their effective service life.
By weight and volume, cubically shaped aggregate is characteristically much stronger than flatter, elongated material. A problem with the existing crushers was their inability to reliably produce aggregate that met the required index of elongation and flakiness. To get the right shape, operators had to recirculate the output product through the crushers, or channel it for additional screening and polishing. Recirculation required additional processing time, which could have been utilised producing new feed material.
Another method employed by the quarry’s team to improve shape was to set the crushers with tighter closed-side settings. This increased downstream plant load, causing the screens and conveyors to use more energy or become overloaded. Running the crushers longer also increased machine wear and energy consumption, and reduced overall production rates. With output quality so heavily dependent on operator intervention, another problem was the constant risk of end-product stockpiles being contaminated with inferior product. The combination of these inefficiencies meant there was also less yield per unit of feed.
Eventually, the Linwood team decided that the installation of two new machines would provide the best solution. After an exhaustive selection process which took into account all of the quarry’s requirements, in 2015 Metso was awarded with a contract to supply two HP3 cone crushers.
Selecting the latest crusher technology
When Linwood first compared Metso HP3’s specifications with the existing crushers, it was a challenge to reconcile their performance and operating requirements. One of the first things that the team noticed was how different the crusher’s size, power and capacity were. The HP3’s design was physically smaller than the old crushers, yet Metso claimed that the machines had a 20% higher-throughput capacity and could produce a higher-precision product with one-pass production.
According to Peter Small, Metso’s capital sales manager, it is the efficiency of the crushing process that makes the biggest difference. “The HP3’s efficiency is derived from a design that increases the concentration of aggregate inside the crusher. It applies more crushing force and relies on a greater degree of interparticle crushing,” he said.
An essential part of Metso’s crushing solution is BRUNO, the company’s crushing and screening simulation software tool. BRUNO calculates and tests process models based on empirical crushing and screening expertise. “Being able to demonstrate the capabilities of alternate configurations and designs gives our customers great confidence in the equipment and the designs we propose,” said Small.
Sailing into unchartered waters
When Linwood needed to select its new crushers, the HP3 had just been released. There weren’t any of these machines operating in Australia, which meant Linwood’s decision-makers couldn’t call upon the experiences of their usual references within Boral or the broader quarrying community. The availability of spares for the first and only units in Australia was also a concern.
Santanu Ghosal, Linwood’s project manager, said, “The benefits were clear to us, but choosing the HP3s was still a leap of faith. Ultimately I think it was the confidence and expertise of Metso’s people that gave us the assurance we needed. We had access to a very responsive team of local and international experts, and had enjoyed great post-sales support with our C140 primary crusher.”
“The support we received helped us to fully explore and understand the options and benefits the HP3s could offer, specific to our situation. For me, a key differentiating factor was the integrated control and automated operation of the HP3s — we knew this was the single biggest technology step towards improving our product quality and efficiency,” said Baker.
Overcoming installation challenges
Replacing the old crushers with the new HP3s was always going to be a challenge while maintaining aggregate production rates at the quarry. From an electrical point of view, the HP3’s larger motor required new mounting and cabling arrangements from the crusher through to the switch room. The mechanical work included installing new cooling units and a bigger stand-alone lubrication system. A redesign of the feeder to a new location was also required. Alongside this work were the site’s safety improvements, which included extended platforms and improved working areas. The team estimated that the electrical and mechanical upgrades would take the tertiary crushing station offline for at least 17 days.
While management planned to stockpile product in preparation for the installation, at the same time they had major projects to supply and knew their reserves wouldn’t last 17 days. In order to help mitigate the loss of production, a trailer-mounted cone crusher and screen was refurbished to supplement supply while the main plant was offline.
A leap forward in site productivity and safety
During the selection process, a high degree of automation was a requirement for the site. Once the new HP3s had been installed, feedback from the quarry’s operators has been particularly centred on this aspect. Mechanical settings, which previously had to be manually adjusted, are now performed in a matter of seconds via the machine’s touch screen. The productivity benefits and the elimination of safety risks involved in manual adjustments have made these features very popular with site operational staff.
Stray metallic objects, called tramp iron, that enter the crusher can stall and even damage the machine. The HP3’s tramp release system with dual-acting hydraulic cylinders and fixed return point lets the crusher easily eject tramp iron. If the crusher stops under load, the dual-acting hydraulic cylinders provide a powerful stroke that clears the crushing cavity. In both instances the crusher’s settings are instantaneously restored without the need for operator intervention.
The HP3’s liner fastening system doesn’t require the backing material that is common with other crushers. When liners are changed or reconfigured, hydraulic motors rotate the bowl completely out of the adjustment ring threads. These two innovations save a lot of time and labour.
Technology upgrade — making the big difference
The upgrades to Linwood’s crushing circuit have improved the site’s production capabilities and modernised its crushing process. Commenting on these outcomes, Baker believes the site is now capable of producing more, while maintaining high-product quality and improving safety.
“The throughput we are getting has surpassed our expectations. Our ongoing maintenance costs have come down, while the automation and access platform upgrades have improved plant safety. Overall, we can now more reliably meet market demands for our key-specification products,” he said.
Phone: 08 9420 5555
Leuze DCR 1048i OCV image sensor
The DCR 1048i OCV from Leuze can read 1D or 2D codes within one application and also check...
Flexicon mobile flexible screw conveyor system
Flexicon's latest mobile tilt-down flexible screw conveyor system is designed for manual...
Cognex DataMan 380 image-based barcode reader
The DataMan 380 barcode reader uses AI and wide-area scanning to speed up production lines.