The ins and outs of isolation: a guide to selecting the right isolator
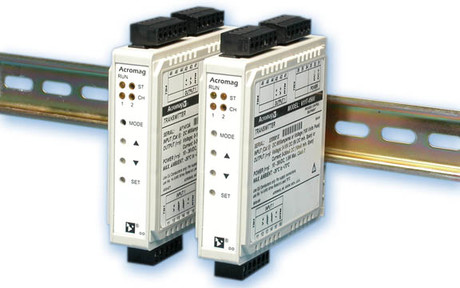
The primary function of the isolator is to eliminate ground loops that may exist between two or more instruments.
A classical application isolates the control room equipment (computers, PLC, DCS etc.) from field devices that may have different ground potentials. In addition to breaking up ground loops, the isolators protect control room equipment from damaging transient spikes and noise generated in the field. Choosing the proper and most cost-effective isolator requires an understanding of the application.
Flat pack isolators are available in 2-, 3-, and 4-wire configurations. Isolators are further classified as input, output, or 3-way (input, output, power) isolators. Input isolation implies that the input signal has no electrical connection to the output and power signals. Output isolation implies the output signal has no connection to the input and power. And similarly, 3-way isolation refers to a situation where there is no electrical path between the input, output, or power.
First we’ll discuss Acromag’s 611T, 330i, and 430i isolators, which provide 3-way (input, output, and power) isolation. They are the safest choice when retrofitting or expanding an existing system. They provide complete isolation when uncertainties about the isolation of instruments in each current loop exist or the grounding scheme is unknown.
The 611T and 330i are DC-powered isolators that operate from an unregulated power supply of 10–36 VDC. The 430i is AC-powered and uses either 115 VAC or 230 VAC. The input loop load of these isolators is less than 1.5 VDC at 20 mA or approximately 75 ohms. These 3-way isolators source current out and do not utilise a separate output power supply. It is important to note that the outputs of these isolators are designed to drive purely resistive loads. Figure 1 shows a typical application for a 3-way isolator.
The primary difference between the 611T/330i and 430i models is the power source. The isolator can be several metres or hundreds of metres away from the PLC or DCS and obtains power from an external AC or DC source. This source may have a different ground potential than the PLC, DCS or field device. If this is the case, the power ground must be isolated from both the input and output. In this example, the isolator input is monitoring a grounded field sensor at a remote site 91 m away. The ground potential at the sensor is likely to be different from the power source and PLC or DCS. Consequently, input to output isolation is also necessary. Additionally, it is important to note that the 611T, 330i, and 430i can isolate 4–20 mA control outputs from the PLC/DCS to field actuators. The PLC/DCS analog outputs are wired to the isolator input and the isolator outputs are wired to the field device or actuator. Although 3-way isolation is the safest and most flexible, it is also the most expensive due to the power isolation circuitry.
Acromag’s compact, DIN rail-mount isolators are available in AC-, DC-, and loop-powered models.
Input isolators
Suppose we relocate the isolators close to the PLC or DCS. The output and power can now share a common grounding point with the PLC or DCS, and 3-way isolation is no longer necessary. But since the input wiring remains the same (see Figure 2), input isolation is still required.
A very cost-effective solution is the Acromag 340i input isolator which provides 250 VAC of continuous isolation from input to output/power. The 340i is ideal for applications requiring multiple isolators at a single location where all isolators share the same power supply. PLCs and DCSs usually have 24 VDC power available at their input terminals. This is ideal for the 340i which operates over an unregulated power supply range of 10–36 VDC. Since the 340i is an input isolator, its 4–20 mA output signal and DC power share a common lead. This common lead should be wired directly back to the PLC or DCS internal ground. Avoid the urge to daisy-chain the common leads between multiple isolators and run a single wire back to the PLC or DCS. Each isolator should have its own ground path back to the monitoring device to avoid inaccurate and noisy measurements. The 340i’s output sources current and does not use a power supply in series with the output signal. Again, the output of these isolators drives purely resistive loads.
Two-wire isolators (current repeaters)
So far we have only discussed isolators that output current to a resistive load. If your application requires an isolator that has a power supply in series with the output signal, this prohibits the use of a 611T, 340i, or 430i isolator so you must use a two-wire transmitter with input isolation. Acromag’s 651T and 250T are two-wire, 4–20 mA input transmitters with isolation and can be considered isolators.
Some PLCs and DCSs are better equipped to handle 2-wire transmitters than other devices. Figure 3 shows a simple connection diagram for the 651T/250T transmitter. Note the output does not go to a purely resistive load: the 651T/250T obtains power from the output loop. Therefore, the transmitter must control current draw from the power supply in the output loop which is the 4–20 mA signal.
Since output and power share the same two wires, these modules can be placed between the field sensing device and the PLC, DCS or monitoring device. A typical configuration is to place the transmitter close to the field device. The 651T and 250T are also ideal as current repeaters. Certain monitoring applications require tapping off an existing 4–20 mA loop to add a measuring or monitoring instrument. This transmitter is ideal for this application because of the low (10 ohm) input load. If the isolator fails or loses power, it will not interfere with the existing 4–20 mA loop. The output of the transmitter/isolator in this application can be wired to a field chart recorder or another PLC to enable redundant monitoring.
Loop-powered output isolators
All the isolators mentioned previously have an input load of 75 ohms or less. Input load is the load the isolator places on the 4–20 mA current loop it is monitoring. Another type of isolator is the loop-powered isolator. This is useful when adding and isolating monitoring instruments to an existing current loop.
In Figure 4, field device #2 is added to the existing loop using a 671T or 270i isolator. No additional power source is required for the added loop or for the 671T/270i. The isolator’s output is powered by the input loop power and only drives passive loads. A drawback of loop-powered isolators is the load induced to the initial loop. The sum of the input voltage loads must remain below the loop power supply capability at full current. Note that an open circuit in the output of the 671T or 270i disrupts the initial loop operation due to increased voltage load. The 671T/270i can also be used as an output isolator for PLC or DCS 4–20 mA outputs.
Unlocking remote connectivity: how LAPP and Tosibox empower industrial VPN access over Starlink
Starlink's use of Carrier-Grade Network Address Translation (CGNAT) presents challenges for...
Pacific Automation delivers exclusive access to Advantech's high-density industrial Ethernet switches
Optimising industrial networking with scalable, rugged, and high-performance Ethernet solutions.
LAPP industrial remote solutions focus on secure remote maintenance and network integration
Through a partnership with German company Helmholz, LAPP Australia is bringing a proven and...