Cobots strong enough to operate in a harsh environment
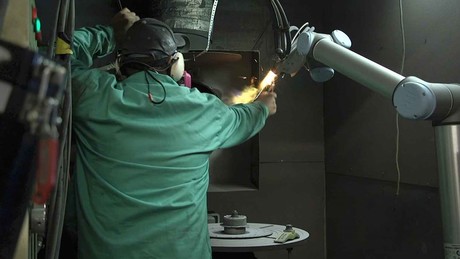
Aircraft Tooling Inc. (ATI), a Texas-based repair centre for the aviation industry, was surprised to find that UR robots could withstand the high temperatures and harsh environment while performing metal powder and plasma spray processes. The cobots have now been in operation for three years without breakdown or service requirements.
Aircraft Tooling has grown from a component-only repair station to include the overhaul of complete landing gear and engine mount assemblies and accessories. The company has continued to maintain exacting standards of quality and workmanship and has become highly regarded throughout the aviation industry. The main objective of ATI’s repair scheme is to restore high-cost parts to new standard dimensions and release for further declared life.
The company was looking into automating repair tasks involving HVOF (High Velocity Oxygen Fuel) and plasma spray-on parts as required within the aviation industry. Juan Puente, thermal spray supervisor with ATI, had initially been recommended to purchase traditional industrial robots but what he found did not meet ATI’s needs. “The cost was outrageous, the cast iron models we looked at were too bulky, we could not easily move them between cells, they were hard to program and all required safety guarding, which would not work in our small spray cells,” he said.
“The UR10 robot had the required reach for the spray distance and the cost was about half of everything else we looked at,” he continued. “It was very user friendly and portable. Because of its collaborative safety features we did not need to fence it in.” He was able to get the UR10 unpacked and programmed in just four hours.
Although Puente readily admits that the UR10 “won their hearts”, there was significant hesitation at ATI as to whether the robot would operate reliably in the spray booth’s extremely hot and dusty environment.
“We were very surprised,” he said. “I actually thought the robot wouldn’t stand it. Some of these powder coatings are tungsten carbide, which is a hard metal coating. If it seeps into the bearings of the robot, we were afraid it would destroy them.”
ATI opened up the seals on the UR10 and found the bearings intact. “There were no particles in there — after three years of operation it doesn’t show,” said Puente, adding that recoil from the spray gun was another concern. “We were nervous that the recoil would trip the robot or interfere with the servo capabilities. We went as high as the pressures would take to make it bounce, and it wouldn’t do it. The robot simply stayed in position.”
Nick Armenta, Automation Engineer with Olympus Controls, the UR robot distributor working with ATI, explained that the company’s experience with the robot’s durability is common.
“We very often see the robots operate in harsh environments, taking over jobs that humans don’t want to perform,” he said. “Many think of cobots as being fragile but the opposite is true, this is an extremely durable robot; it’s sealed against dust, rated for high temperatures and works just as well in extreme environments as in a cleanroom.”
ATI was also surprised to find that no preventive maintenance is required with the UR robots. “All we do is dust the robot arm off and keep on going,” said Puente, adding that he did not have to pay for a licensing or service agreement. “That was really unusual compared to other solutions we looked at. With the UR robot, everything was included in the purchase price.”
Excelitas pco.horizon 9.1 bi TDI CLHS Line Scan Camera
The pco.horizon 9.1 bi TDI CLHS Line Scan Camera is designed for precise inspection applications...
ABB IRB 6730S, IRB 6750S and IRB 6760 large robots
ABB Robotics is expanding its large robot range with the launch of the IRB 6730S, IRB 6750S and...
ABB IRB 1200 industrial robots
ABB Robotics is releasing a new generation of its IRB 1200 small robot range that it says is...