Cobots improve palletising and ergonomics at Unilever
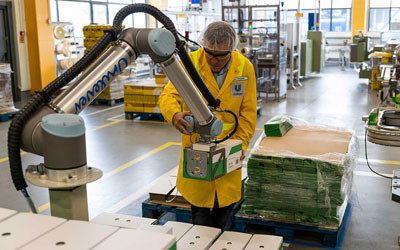
Unilever is one of the world’s largest companies within the fast-moving consumer goods (FMCG) industry and the owner of around 400 brands, available in over 190 countries. The company has four production plants in Poland. One of them, in the town of Katowice, specialises in packing tea delivered to the factory in 25 kg sacks.
The plant employs around 400 people working in two production halls. Dariusz Ratajczak, Automation Senior Specialist at Unilever, explained that for a long time the company faced difficulties in keeping and finding employees for monotonous, manual tasks related to packaging and palletising — tasks that were often also strenuous due to the product sizes handled. Unilever needed a solution automating these processes; however, finding a flexible robot with appropriate payload and reach, as well as intuitive handling and programming was challenging. Particular tasks were to be divided into sub-processes in order to systematically automate individual phases, freeing people from strenuous tasks and involving them in more value-added ones.
“Each year a decreasing number of people apply for positions related to palletising but in our plants this is a key process which has to be performed efficiently,” Ratajczak explained. “For packaging we needed a robot with enough reach of the arm. The task that the robot needed to fulfil consisted of picking various boxes with tea and placing them on a pallet.”
Unilever automation specialists had considered a ready-to-use solution such as palletising robots. Taking the pros and cons into consideration, the team decided that cobots would be more flexible and easier to use — and would deliver a quicker return on investment.
“We considered many solutions, but finally we decided to test robots by Universal Robots,” said Dawid Mroczek, Automation Specialist at Unilever.
The UR10 cobot, with a reach of 1300 mm and payload of 10 kg, was comprehensively tested in the Unilever plant. While performing the task of tea packaging, a vacuum gripper was used. The tests went well and so the company decided to go ahead and deploy them. Implementation of the first cobot was done by the Biuro Inżynierskie IEC company and took around three weeks. The basic training for the automation team of Unilever related to programming of robots was given by the local distributor of UR cobots, Encon-Koester.
Unilever fully automated two production lines in Katowice where six UR10 robots now handle tasks related to packing of the tea. Before implementing automation, all these tasks had been performed by a human. Operators spent around 70% of the time packaging and 30% palletising. With the palletising now entirely automated by the cobots, the operators have been freed up from 30% of the tasks. Cobots perform the most tiresome work and are also very efficient, palletising around 1100 boxes during an eight hour shift.
“Implementation of the first UR cobot took about three weeks,” Mroczek recalled. “Now it can be deployed in just a few hours. The programmer’s task is to define the boxes’ picking points and boxes’ sizes.”
The robots’ programming depends on the shape and size of cardboard packaging. However, in all cases this process is similar. After reaching the specified number of boxes on the pallet, the UR10 starts the next layer. The pallet usually contains six to 10 layers and has 10 to 21 boxes in each layer. When the packaging process on one layer is completed, the cobot calculates the new height and marks the starting point for the next one. When the operator notices that the UR10 begins to stack cartons on the next pallet, he departs with the already loaded pallet. Completing the pallet takes a cobot about 20 to 30 minutes.
“My first experience in robot programming was achieved through the UR Academy website,” Mroczek said. “In our team, we exchange experiences and systematically increase the complexity of the functions used with more advanced scripting programming. Programming at the basic level is extremely intuitive. Currently, we use mainly advanced scripting programming, because it allows us to speed up and unify the creation of programs which is achieved by defining ramps and sizes of boxes in the program.”
“Deployment of UR10 cobots enabled us to reduce the packaging time while improving the work ergonomics considerably,” Ratajczak said. “Before automation, employees had to perform monotonous tasks involving bending over to place boxes on lower layers of the pallet. This most difficult activity was totally eliminated by the UR robots.”
Implementation of collaborative robots is also being considered at other Unilever plants with automation specialists from Katowice willing to share their experience, explaining how they solved the palletising problem with cobots. The Katowice team also works on automating the process of depalletising, enabling the cobots to pick materials for production.
Phone: +65 6635 7270
Excelitas pco.horizon 9.1 bi TDI CLHS Line Scan Camera
The pco.horizon 9.1 bi TDI CLHS Line Scan Camera is designed for precise inspection applications...
ABB IRB 6730S, IRB 6750S and IRB 6760 large robots
ABB Robotics is expanding its large robot range with the launch of the IRB 6730S, IRB 6750S and...
ABB IRB 1200 industrial robots
ABB Robotics is releasing a new generation of its IRB 1200 small robot range that it says is...