Modular connectors — the backbone of a smart factory
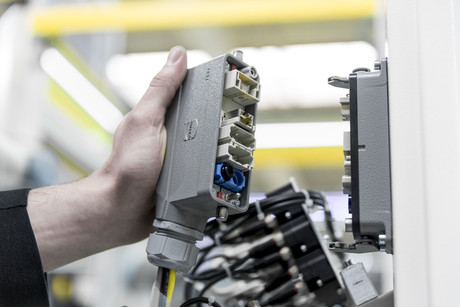
Industry 4.0 and the associated dramatic changes driven by the development of smart factories — which are resulting in the modularisation of machines and plants — are seeing the connector undergo a fundamental transformation.
Whereas decentralisation was a structural change in deployment, and installation technology driven by the manufacturer of machinery and plants, modularisation is a user-initiated change brought about by the need for greater flexibility. Modularisation has implications beyond the traditional responsibilities of employees. It first and foremost impacts the plant operator interested in configuring the plant in the simplest way possible. The task here no longer lies with the automation expert or the maintenance engineer — rather, it is the operator who wants to use a more simple ‘plug-and-produce’ system. This has a fundamental impact on the connector, since it now becomes an integral part of a smart infrastructure.
The market standard for modular connectors
With the Han-Modular series, users can optimally design connectors to supply machinery and equipment. This is made possible by combining individual modules for different transmission media. The connector handles different signal types through the combination of different modules that the designer selects. Modules can also be used to accommodate multimedia types — power, signal and data can be combined into a single connector rather than separate connections.
Endless combination possibilities
Future smart factories will be much more transformation-capable than today’s factories. Mass customisation will demand the production of individual products using mass production standards and efficiency. This goal can only be achieved if production can be continuously adapted to individual requirements as fast as possible. A modular connector with standardised interfaces is consequently a requirement.
However, enhanced requirements arise when a connector is no longer part of the installation but becomes the standardised infrastructure interface. In a smart factory there is no traditional commissioning that ends with a standard system configuration. In principle, a smart factory is continuously commissioned over and over again in operation, or a reconfiguration takes place, even during operation.
All the associated possible configurations cannot be tested in traditional commissioning. This has a number of ramifications, not least of which is that the new configuration must be able to be produced easily and securely, and it cannot be assumed that specially trained personnel will be available for this purpose.
The gateway to the IIoT
The latest expansion of the modular series is the introduction of Smart Han modules that allow connection to the Industrial Internet of Things (IIoT) at the connector level. HARTING combines expertise in reliable connectivity with future-forward technology — in the footprint of the well-established Han-Modular insert.
HARTING’s Smart Han approach is to develop solutions in conjunction with leading IIoT thought leaders, as needs arise, with the goal of making them globally available.
Seamless modular I/O integration
For seamless modular I/O integration, WAGO controllers combine with WAGO's I/O System 750 to...
LAPP Australia introduces ultra-reliable Wieland Electric wipos power supplies to Australia
Power supplies perform a central function in the control cabinet, so a robust and proven design...
Drive the future of transportation with SCHURTER
SCHURTER offers solutions for various applications in the automotive industry: our products...