Industry 4.0: Futureproofing workflows and supply chain management
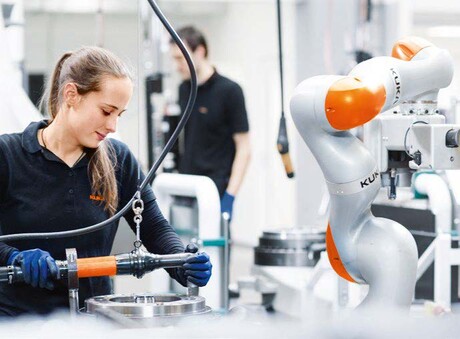
Those manufacturers who had integrated IIoT technologies into their operations before the onset of the pandemic were less affected by the resulting disruptions.
The instability and disruption brought on by the COVID-19 pandemic exposed vulnerabilities in the Australian manufacturing sector. These primarily relate to issues around labour shortages and volatile supply chains.
Less affected by these widespread disruptions were those manufacturers who had integrated Industrial Internet of Things (IIoT) technologies into their operations before the onset of the pandemic.
The pandemic has seen a high demand for the IIoT to help ensure business continuity and better remote monitoring. In addition, it’s been used to reduce the risk of COVID-19 outbreaks by allowing staff to work from home and to practise safe social distancing.
The members of the Open IIoT Group, a cohort comprising of some of Australia’s most prominent automation companies such as SMC Corporation ANZ, Beckhoff Automation, NORD DRIVESYSTEMS, Balluff, ZI-Argus and KUKA Robot Automation, observed a spike in those seeking Industry 4.0 implementation on the factory floor as the pandemic wore on.
Rethinking supply chain management
Borders closing and countries going into lockdown exposed the vulnerability of global supply chains and the need to ‘reshore’ manufacturing by strengthening local supply chains. This enhances local capabilities and protects the sector against future disruptions.
Future-thinking manufacturers are decentralising their production, building up a network of second-source suppliers, increasing their local stock and working on continuously improving their supply chain.
To improve their supply chains, manufacturers are encouraged to re-evaluate their current systems and the ability of these systems to adapt to rapid changes. The strongest supply chains are functional, digital and crucially, flexible.
Industry 4.0 implementation, along the supply chain and in the digitalisation of processes, promotes flexible manufacturing and helps meet increased demand from local customers. The challenge of changing a production line to produce more units, multiple variations or a completely different product at a rapid speed has called for the consideration of modular and scalable production lines.
A supply chain that is flexible enough to respond to changes and react to production demands requires traceability and real-time visualisation. Industry 4.0 enabled technology such as RFID systems, barcode information and software integration into ERP systems are a critical part of achieving this goal and can be implemented relatively easily.
Futureproofing workflow with automation
In the context of the manufacturing sector, ‘workflow’ refers to the series of activities that are necessary to complete a task. Each step in a workflow has a specific step before it, and a specific step after, and there are various workflows across the entire manufacturing supply chain.
To avoid costly disruptions, it is necessary that the workflows be as efficient and resilient as possible to ensure continued operations and production. The most significant threat to workflow in Australia is labour shortages due to employees who either lack the skills or the desire to perform their tasks in the workflow. This challenge looks set to continue even once the pandemic is under control, with labour shortages affecting every sector.
One possible ‘futureproof’ solution involves fully automating manufacturing processes. Certain industries, such as those in the distribution of fast-moving consumer goods (FMCG), have been using fully automated warehouses for many years, with automation proving to be far more reliable and timelier than those using traditional manual pick-and-pack methods. By harnessing the power of live-data and automated picking machines, the process of getting goods out the door, safely and accurately, benefits both the consumer and the supplier.
In manufacturing, automation via the use of robotics has become a relatively easy ‘go-to’ to improve production, address labour issues and help companies stay competitive. Increasingly affordable and simple to program, collaborative robots have stepped up to the plate, performing flexible movements that can replace the boring and monotonous tasks previously done by people. The beauty of this type of automation is its ability to offer flexibility, as the same cobot can be used for multiple functions. Automation also allows for the possibility of 24/7 operations, without having to consider workforce management or overtime costs.
How to get the ball rolling
The wide range of IIoT solutions available can be tweaked to suit the individual needs of a manufacturer. However, before supply chain and workflow challenges can be addressed, manufacturers need to identify a simple starting point for Industry 4.0 implementation.
We suggest following these seven steps to get the ball rolling and start sooner than later:
- First, consult with Industry 4.0 experts to get a better understanding of what the process will entail, and the costs involved.
- Identify the areas in your current processes that will directly benefit from an Industry 4.0 solution and create KPIs for these areas to measure the success of the implementation.
- Generate a scope of work for implementation and break it into phases, with each successful phase leading on to the next.
- Engage Industry 4.0 experts to implement these phases and monitor changes in each area.
- Educate existing staff members on the purpose of implementation and the tools needed to use the solution.
- Continue to measure to ensure the solution is still making an impact on the process and production.
- Finally, be flexible when it comes to budgeting for an implementation — in time these solutions will pay for themselves. Consider an operation costing model to support ongoing development and implementations rather than a traditional capital costing model.
About the Open IIoT Group:
Empowering industries through pioneering training solutions
HYDAC's training program is about more than ticking boxes — it's about building...
METTLER TOLEDO to showcase solutions at ROKLive in July
METTLER TOLEDO is preparing to showcase its weighing solutions and process analytics...
Safety and security in transformation
The integration of industrial security into machinery safety is not a distant concept but a...