Intelligent rotor blade optimises wind energy utilisation
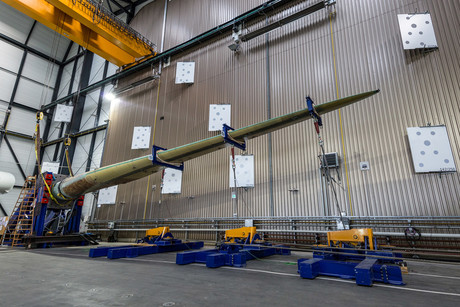
The share of the overall electricity market made up by wind energy continues to grow year after year, and the giant rotor blades utilised are one of the most important parts of a turbine
More than 28,000 wind turbines with a total output of 50 GW are currently in operation in Germany. This equates to a 12.3% of the total electricity production in Germany in 2016. The current focus of research is now on developing this technology even further.
Within the framework of the joint SmartBlades2 project, the Fraunhofer Institute for Wind Energy Systems IWES and its partners have turned their attention to the bend-twist coupling (BTC) concept for rotor blades. The passive working coupling adapts continuously to the wind forces acting on the rotor blade. When the wind loads become too high, the bend-twists reduce the forces affecting the structure.
The rotor blades of conventional wind turbines react to changing wind strengths very slowly. A rotor blade measuring up to 85 m in length describes a circular area of 22,670 m2: the equivalent of four soccer pitches or St. Peter’s Square in Rome. The wind strengths within this area can vary greatly. The pressure acting upon the blade pointing upward, for example, can be very different from the pressure on the lower blade. Conventional rotor blades cannot compensate for a single gust of wind as they are too rigid to twist. This means if there is a gust when the wind is already strong, the turbine operators turn the rotor blades completely away from the wind, resulting in long downtimes during which no electricity is produced.
“The demonstrator BTC blade developed as part of this project is swept back, while the blade tip is offset slightly to the rear in the direction of rotation,” explained the IWES technology coordinator for BTC blades, Dr Elia Daniele. “The 20 m long rotor blade is therefore able to rotate slightly around its own axis should strong gusts occur, in order to mitigate the wind pressure to a certain degree.”
This ability reduces the forces acting upon the blade and, ultimately, the entire turbine. By using BTC blades on a newly planned wind turbine, the overall turbine weight can be reduced as the structure is subjected to lower loads. In the case of existing turbines, the retrofitting of BTC blades allows the rotor diameter to be increased without having to adapt the other turbine components. This results in an increase in revenue due to a greater wind yield.
To test this innovative design, static and dynamic tests are being conducted on the Fraunhofer rotor blade test bench in Bremerhaven over a period of several weeks. The test engineers have installed a BTC blade for the first time here. The blade was designed by Fraunhofer IWES and produced by the project partner German Aerospace Center (DLR). Its durability when subjected to extreme loads will be tested in static tests.
“Although the setup for the rotor blade torsion test is similar to the conventional scenario for static testing, it is in fact more complex, as the additional deformation has to be measured precisely,” said IWES test engineer Tobias Rissmann.
Deformation along the three main axes is monitored using a visual measurement system. Angle sensors were also used to ensure that the force was introduced vertically to the blade axis. During the subsequent dynamic tests (fatigue tests), the stresses incurred over the entire service life of the rotor blade spanning 20 years are simulated within a drastically reduced time frame.
Upon completion of the test bench testing, three identical BTC rotor blades will be transported to the USA to be installed at the foot of the Rocky Mountains for a field test on a research turbine from project partner National Renewable Energy Laboratory (NREL). The aim of subsequent measurements, which will be led by Fraunhofer researchers, is to demonstrate whether passive twisting performs as expected in real, open-air operation.
The Aeroprobe System, which has been newly developed as part of this project, will also be used for testing. In this system, two pressure sensors on the surface of the blade measure the flow dynamics around the rotor blades. The flow on the rotor blade is also made visible by strands of wool. This allows the experts at Fraunhofer to determine the aerodynamic conditions precisely. Within the blade, further sensors work to measure the acceleration at the blade tips while camera-reflector systems detect any deformation.
Fraunhofer IWES is not planning to design rotor blades itself; instead, it is focused on developing its expertise in this field and making this available to its industrial partners. The BTC blade serves to demonstrate the technology and assess the usability of this technology on commercial blades.
Mettler Toledo oxygen measurement guide
Mettler Toledo has produced a guide for the process industries that explains the measurement...
Mettler Toledo pH sensors operating guide
Mettler Toledo has released a booklet describing good operating procedures for pH sensors, aimed...
Honeywell Process Solutions LEAP project services
Honeywell Process Solutions has launched its LEAP project services (Lean Automation of Automation...