Scalable automation solution optimises process at kaolin processing plant
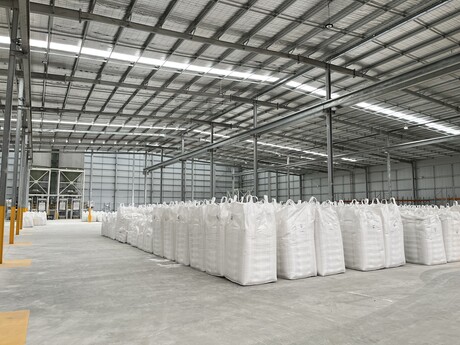
A new kaolin mining operation in Wickepin, Western Australia, is utilising an integrated automation solution to reduce overall costs, improve scheduling and deliver ongoing benefits to operations.
Kaolin, which is becoming increasingly valuable, is a soft white clay that has been surging in demand, with uses in applications including paper and plasterboard, ceramics, fibreglass, paints and coatings, plastics, rubber, pharmaceuticals and medicine, cosmetics, concrete construction materials and agriculture.
WA Kaolin — an ASX-listed mineral exploration, extraction and processing company — has developed a proprietary dry processing method known as K99, which turns raw material into market-suitable feedstock for global customers.
Combined with the high quality of the ore reserve, the K99 process delivers high-quality, ultra-bright kaolin at a lower cost than conventional chemical bleaching and magnetic separation processing.
WA Kaolin has constructed a Stage 1 commercial processing plant on a three-hectare site in Wickepin, about 200 km southeast of Perth, Western Australia. The site has been identified as having a mineral resource estimate of more than 600 million tonnes of extremely high-grade, easy-access kaolin across its mining and retention tenements, one of the largest known remaining premium primary resources of kaolin in the world.
“In late 2022, WA Kaolin successfully commenced production at the Wickepin Kaolin Project following a challenging development timeline,” said WA Kaolin Chief Executive Officer Andrew Sorensen. “Since then, we have continued to ramp up production to our Stage 1 capacity of 200,000 tonnes of kaolin per annum and commenced planning to increase output at Wickepin towards our Stage 2, 400,000 tonnes per annum target.”
WA Kaolin selected engineering and planning consultancy Willyung Electrical & Controls Engineering (WECE) to manage the process of steadily scaling up. WECE is a WA-based specialist supplier of electrical engineering and control systems integration services for industries including agriculture, forestry, food and beverage, materials handling, mining, water and wastewater.
“After analysing WA Kaolin’s robust and ambitious scale-up plans, we determined that Rockwell Automation had the best automation solution for the project and for the future,” said Chris Bock, Managing Director and Principal Electrical Engineer, WECE.
WECE selected Rockwell Automation’s PlantPAx DCS to provide a single, plant-wide control system, with the flexibility to make better and faster business decisions and a scalable solution for future expansion. The PlantPAx DCS will monitor and run the facility from a single point of control, providing seamless integration into control and power systems, and outputting data that is easy to analyse.
The latest version of PlantPAx DCS has been designed to be an integral part of a digital transformation strategy that boosts productivity and profitability, while reducing operational risk.
“Large projects like the WA Kaolin Wickepin processing plant are complex, and it’s easy to come in over budget or off schedule if the right automation technology isn’t implemented upfront,” said Raj Singh, Channel Manager, Rockwell Automation. “WA Kaolin has taken an intelligent approach by seeking to optimise scheduling and reduce overall costs from the beginning. The cost of a poorly designed control system typically only shows up later in the project, when it’s at its most expensive to address.”
By integrating process, power and information across the plant right from the outset, WA Kaolin was able to achieve a faster time to market, and the system can readily be scaled up as production increases. The plant is currently in production with expansion processes in progress, and with the new DCS in place, WA Kaolin and WECE estimate it will save 20% on costs and achieve a 15% schedule reduction.
The solution also included zero touch computing technologies from Stratus Technologies.
“Working alongside Rockwell Automation and Stratus, Willyung Electrical & Controls Engineering has delivered this solution at the Wickepin Kaolin Project with positive results,” Sorensen said. “Importantly, the control system is a scalable solution and supports WA Kaolin’s strategy to rapidly increase capacity from the processing plant without downtime over the coming years.”
Phone: 03 9757 1111
Direct Automation CM5 HMI series
The CM5 HMI series offers high-performance HMIs in six screen sizes from 4 to 22 inches.
Rotork IQ3 Pro valve actuator
The Rotork App provides control and communication capabilities for the IQ3 Pro and is designed...
GEA T.VIS E-20 control top
The GEA T.VIS E-20 control top is suitable for industries that process highly flammable hazardous...