A boost for safety and speed
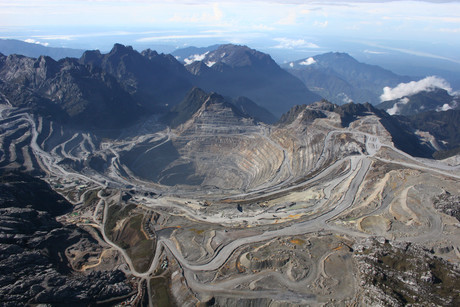
The atmosphere in underground mines is anything but pleasant, with hot, noisy and tight quarters. No matter how vigilant workers are about safety, risks abound. So when planning the underground mining operations at the Grasberg mine in Papua, Indonesia, owner Freeport-McMoRan Copper & Gold wanted an alternative that involved as few people in this hostile environment as possible. The company’s search brought it to the Kiruna mine in Sweden.
In Kiruna, underground mining has been carried out remotely since 2012. Operators work in an air-conditioned control room — their connection to the underground mine is via a screen and a joystick to control the machinery. In the end, Siemens’s automation solution partner, Midroc — the company that implemented the underground mining solution for the Kiruna mine — was contracted in 2015 to install a similar set-up in Indonesia.
Since 1973, Grasberg has been operated as an open-pit mine. However, the open-pit mine cannot be made any deeper and operations must now go underground. The effort is well worth it: Grasberg contains the world’s largest gold deposit and the third-largest copper deposit.
“The underground operations are currently in different stages of implementation,” said Mark Yseboodt, sales development manager for mine automation at Siemens.
The first is the block cave mine. Block cave mining is a highly efficient form of underground mining: large ore blocks are cut from beneath, allowing the ore to collapse under its own weight. After collapsing, the ore is brought to loading points and conveyed to a crusher. The crushed ore is then loaded onto driverless trains and transported to an unloading station, from where it is brought up to the surface.
To put the extent of the operations in the block cave mine into perspective, there are 20 chute galleries with a total of 121 loading points and nearly just as many crushers, plus three unloading stations. Eleven production trains and five service locomotives travel 28 km of electrified rail. A CCTV system with 220 cameras allows operators in the control centre to monitor all activities in real time. At peak production, the mine will produce 160,000 tons of ore per day.
The automation system, based on Simatic PCS 7, connects the underground equipment to the operators in the control room: the chute galleries, unloading stations and service area including the motor control centre (MCC), variable frequency controllers (VFC), uninterruptible power supply (UPS) and CCTV. As in Sweden, the operators are able to monitor and control a range of activities in a comfortable and, most importantly, safe environment. For example, the chutes and crushers are driven from the control room, as well as the train movements.
“A special aspect of Simatic PCS 7 is that it has interfaces to all equipment, even equipment from third parties,” said Yseboodt. A case in point is the Bombardier train system being installed in the mine. From their screens in the control centre, operators have direct access to the train automation system without having to change screens or even the user interface.
Creating a safe environment was a key concern for Grasberg’s operators, and the communication system delivered by Siemens is a key component. While some of the communication between the control centre and the devices is wired, for the most part wireless networks are employed.
“In an operation like a mine, you can’t afford any mistakes or errors. The communication system has to work at all times,” said Yseboodt. For this reason, all systems feature double redundancy. For wireless communication, rapid roaming has been employed, allowing the mobile devices to roam between access points within 50 ms.
The next stage is the deep mine lower zone. The mine is half as large as the block cave mine but in many ways similar in its set-up. However, instead of unmanned trains, conventional trucks are employed for ore transport within the mine.
Simatic PCS 7 is not only being put into service for mining operations: the third area is for a common infrastructure project. The focus is on traffic control and ensuring safety for truck and bus movements and for two tunnels.
In line with Grasberg’s wishes, the delivered solution is basically the same as the one in Sweden. The biggest difference is in the communications networks.
“In the five years since operations started in the Kiruna underground mine, the amount of data that has to be transferred has grown exponentially,” said Yseboodt. “The rapid roaming access points in the wireless communication network have been adjusted accordingly.”
Grasberg is getting a solution that fits the bill in more than one way. Not only is worker safety improved because fewer people are exposed to unsafe situations, the solution also brings more speed. And that’s good for the bottom line.
Phone: 137 222
Direct Automation CM5 HMI series
The CM5 HMI series offers high-performance HMIs in six screen sizes from 4 to 22 inches.
Rotork IQ3 Pro valve actuator
The Rotork App provides control and communication capabilities for the IQ3 Pro and is designed...
GEA T.VIS E-20 control top
The GEA T.VIS E-20 control top is suitable for industries that process highly flammable hazardous...