IO-Link technology: capabilities, limitations and benefits
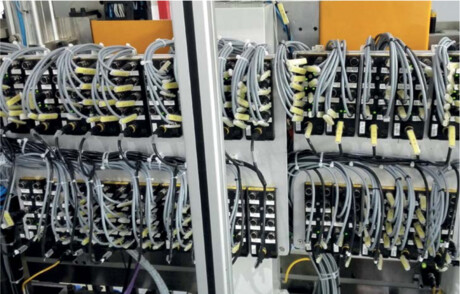
From parameter storage to detailed diagnostics, IO-Link’s advanced features and functionality have generated plenty of excitement. However, this intensive focus has created the common misconception that advanced capabilities are the only reasons to implement this technology. The primary goal of IO-Link is to improve sensor or field-level device communication capabilities through a standardised interface. This goal is not only relevant for complex installations or operations. It is also useful for simpler applications found in many automated systems. Engineers often implement IO-Link to improve essential functions such as data processing. They can also achieve higher I/O density, standardise interface technology and improve capabilities compared to traditional I/O systems.
IO-Link makes seamless, point-to-point communication possible down to the sensor level — and Turck makes it easy. With a wide breadth of automation products that fit nearly anywhere they are needed and drag-and-drop implementation, Turck takes the complication out of implementing solutions with IO-Link. With no extra software required and no extra changes using a web server, the products are ready for all major PLC platforms.
While it is now possible to implement this technology in most modern automated control systems, not every application is an ideal fit. By understanding IO-Link — both its capabilities and its limitations — automation systems engineers can decide if it is a worthwhile investment for their company.
IO-Link overview: How it works and the benefits it delivers
IO-Link is a point-to-point communication protocol between a field device like a sensor, actuator or I/O hub, and an IO-Link master. The data is generally transmitted from the IO-Link master device via a higher-level fieldbus communication protocol (whether industrial Ethernet or a serial-based fieldbus) to a PLC or industrial computer. IO-Link is manufacturer and fieldbus independent, allowing it to be implemented across a large variety of higher-level fieldbus protocols and product platforms. This delivers a benefit to engineers because they can standardise on a single sensor interface, creating uniform integration across many field-level devices. IO-Link becomes the unified tool for configuring complex sensor devices or simply communicating data back to the PLC.
In analog systems, connectivity components must be robust to eliminate interference. IO-Link is standardised to utilise inexpensive 3-conductor, unshielded M12 cables. This eases integration into the larger system, as one type of cordset can replace various analog and proprietary cables. The cost benefit continues to grow with the complexity of a system, especially in high-density I/O situations. Another fundamental advantage of IO-Link is simplified commissioning and replacement of complex I/O devices. The configuration and parameter data of IO-Link devices can be viewed, changed and stored via simple-to-use software configuration tools or directly through the PLC. This reduces labour-intensive manual configuration and ensures that the correct parameters are programmed on devices every time. Using the parameter storage function of the IO-link master further simplifies configuration of new devices during a change-out. It automatically pushes the stored parameter data to the newly connected device. Engineers also turn to IO-Link to improve data quality.
As a universal digital communication interface, IO-Link represents what would traditionally be transferred as analog or discrete data. In analog systems, data collected at the sensor level must go through multiple analog-to-digital conversions before reaching the PLC. IO-Link reduces the number of conversions required to one at the sensor itself, thereby limiting accuracy losses.
When to use IO-Link
The sheer number of IO-Link use cases make it impossible to come up with a one-approach-fits-all solution, but the application challenges below will help in identifying how IO-Link might benefit you. For example, say your I/O needs are changing, but PLC upgrade options can be inflexible or limited in I/O density. I/O points can be expensive when it means upgrading or purchasing a PLC. By implementing IO-Link master fieldbus nodes, IO-Link-capable sensors, actuators or hubs can be combined as needed to create high-density or mixed I/O systems without needing to change the PLC’s capabilities. And because IO-Link is a point-to-point protocol, each IO-Link master port can connect to a single sensor or IO-Link hub. By combining a variety of IO-Link field devices as needed, companies can gather the required data from end devices throughout the plant. The data is then transferred via a fieldbus network from the IO-Link master to the PLC.
The future of IO-Link
As the number of installed IO-Link devices has stretched into the millions over the past decade, new updates seek to unlock even more capabilities. One of the biggest updates for IO-Link came in 2017, when the IO-Link Community released its specification for IO-Link Safety. Until this specification, there was no standard for implementing safety over IO-Link.
The new standard has opened the door to the future of IO-Link for industrial applications. New safety I/O devices will be introduced that communicate safety signals directly over IO-Link. These devices will extend the advantages of IO-Link into functional safety systems by facilitating high-density safety I/O hubs, simplifying wiring, and seamlessly implementing more complex safety sensors. IO-Link also continues to be an important enabler technology for the Industrial Internet of Things (IIoT). As companies look to connect all areas of the plant for real-time data, insights and analytics, IO-Link can reliably communicate exactly what is happening at the device level. By implementing this capability now, companies can prepare themselves for the IIoT.
For more information go to https://www.turck.us/attachment/B1905.pdf.
LAPP industrial remote solutions focus on secure remote maintenance and network integration
Through a partnership with German company Helmholz, LAPP Australia is bringing a proven and...
The gateway to safe and flexible PROFINET connection
LAPP Australia is introducing the Helmholz range of industrial automation equipment to Australia,...
Interference doesn't stand a chance with LAPP cables that ensure electromagnetic compatibility
Suddenly, the robot stops: When searching for the cause, very few people think of interference...